SPHERE OX – THE SOLUTION TO CASTING DEFECTS
If we talk about defects in the foundry, we would create quite a long list. SphereOx is being considered, in conversations within Euskatfund, as a possible solution. We explain what we mean in this post.
THE DAILY STRUGGLE OF THE FOUNDRIES
⇒ The causes of defects
Veining, burnouts, penetrations and pinholes are common defects in castings, and foundries struggle to control them on a daily basis. Unfortunately, many variables can contribute to the cause of the defect, starting with the choice of sand.
Due to cost, silica sand is commonly used as the aggregate of choice, but pure silica sand expands by an average of 4 – 5%. When molten metal enters a mould, a brutal thermal shock to the sand occurs and is followed by rapid expansion of the sand. This flexible contraction/expansion causes the core matrix of the bonded sand to fracture and break, causing veining defects. Although there are other options to silica sand that offer lower and more controllable expansion rates, such as zirconium and olivine sand and chromite, their cost is almost 10 times higher. Even when more stable sands are used, it is still possible to find veining defects and scaling in castings because there are also other variables, such as compaction and sand particle size distribution, that need to be controlled.
SYNTHETIC IRON OXIDE SPHERE OX
⇒ IRONS AND STEELS
Highly alloyed irons and steels (e.g. high levels of chromium) will cause base metals to have lower viscosities. Castings made from these types of alloys are more prone to veining. High casting temperatures of the molten metal also promote veining and penetrations.
Auxiliary products – Synthetic iron oxide Sphere Ox
⇒ RESINS
Resins are formulated to provide greater adhesive strength rather than cohesive strength. The more resin used, the stronger the core and the less chance of breakage during handling and transport.
Excess resin does not allow the core to be plastic enough to allow the sand to expand, causing the core to fracture causing molten metal to enter the mould.
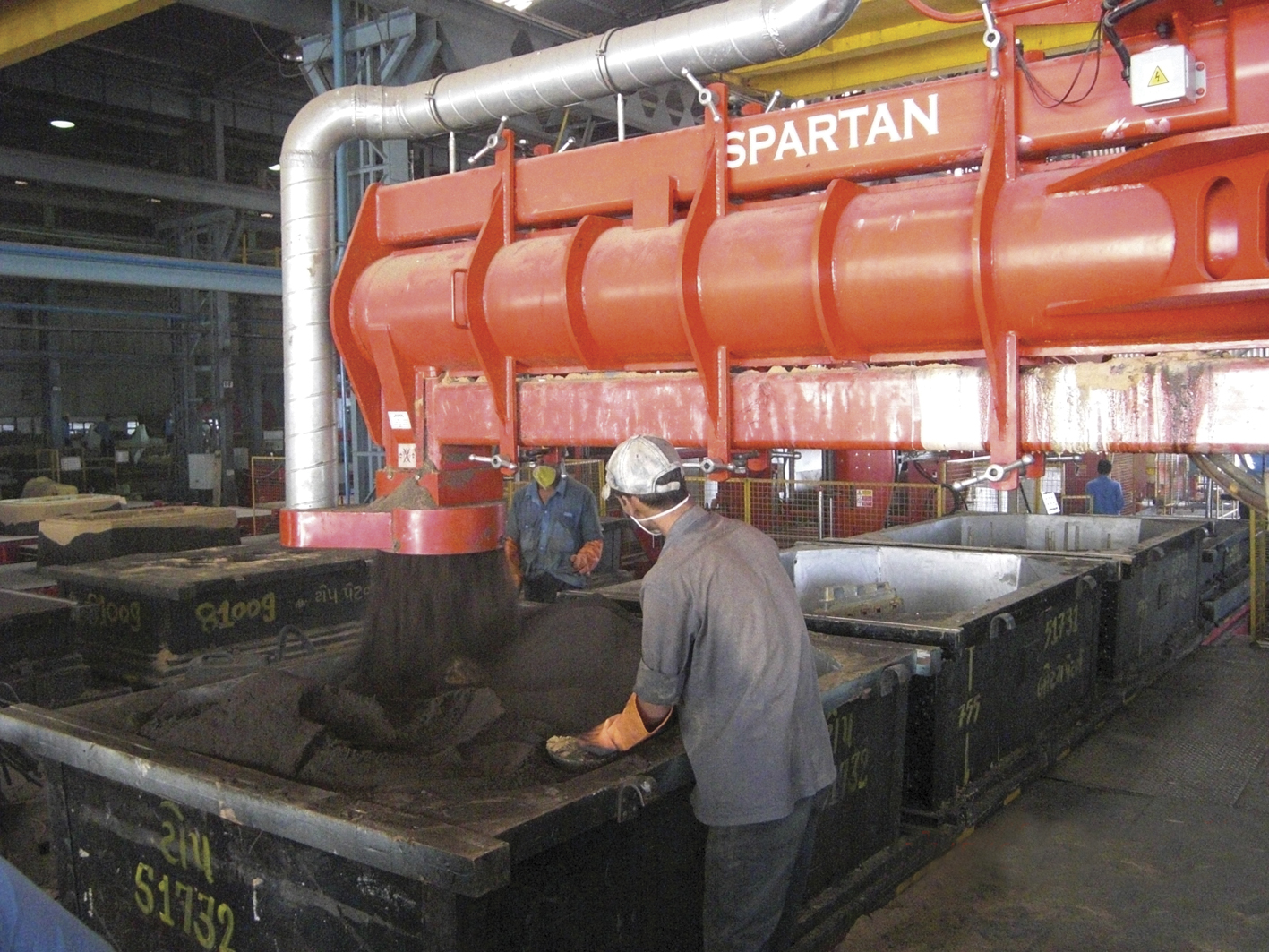
The choice and amount of resin used to bind the sand in a core, or mould, is very critical. When trying to limit or eliminate negative influences on its use, calcines, pinholes and other gas related defects are taken into account. When the resin burns, voids are created where the resin was.
The molten metal penetrates into the voids and the part suffers from calcination defects. Pinhole defects are created when the gas generated by the burning resin (in the mould or core) cannot escape before solidification. Ideally, enough resin should be used to eliminate core breakage, but not so much that the core is so hard that it can be broken by the thermal expansion that takes place, breaking the cohesive strength of the resin.
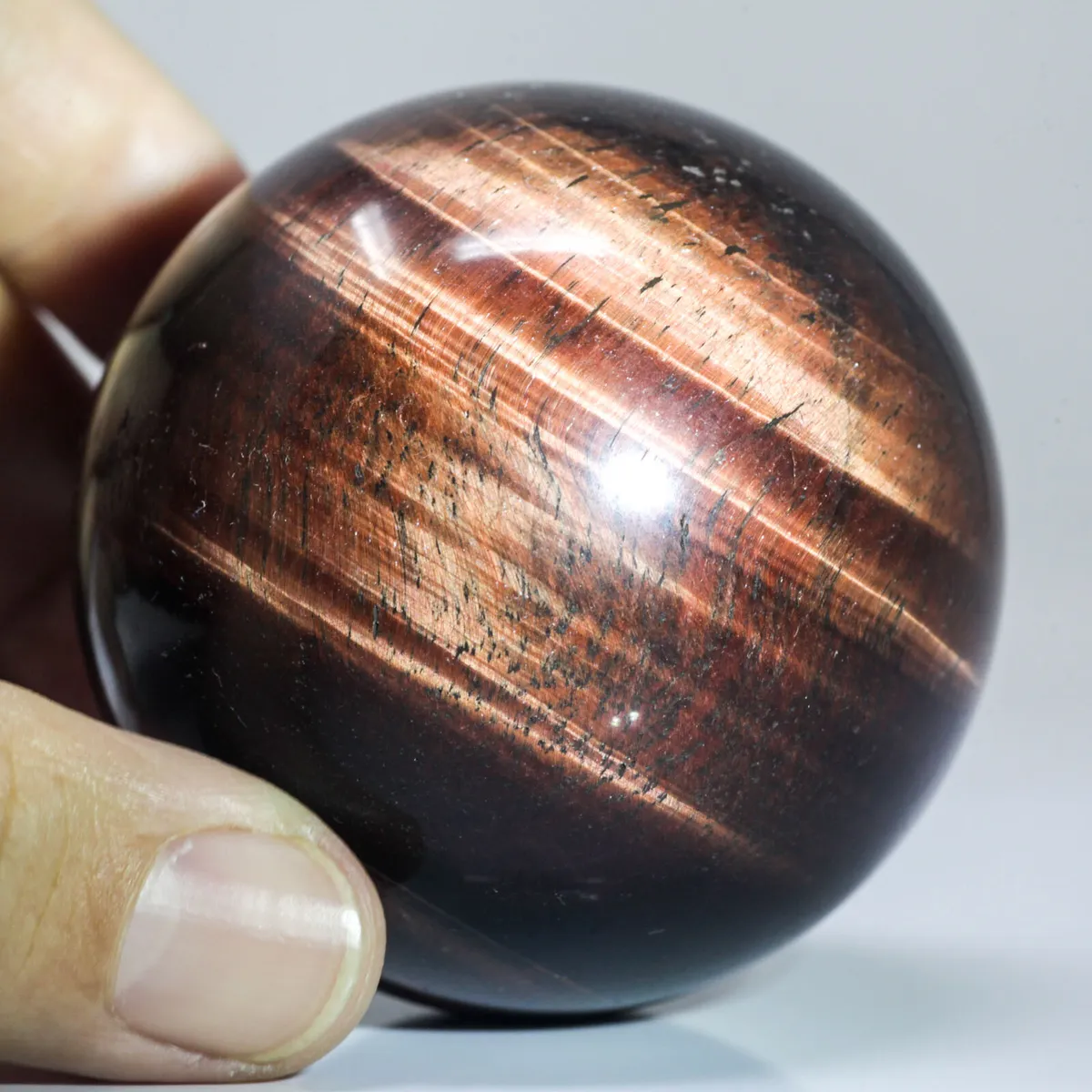
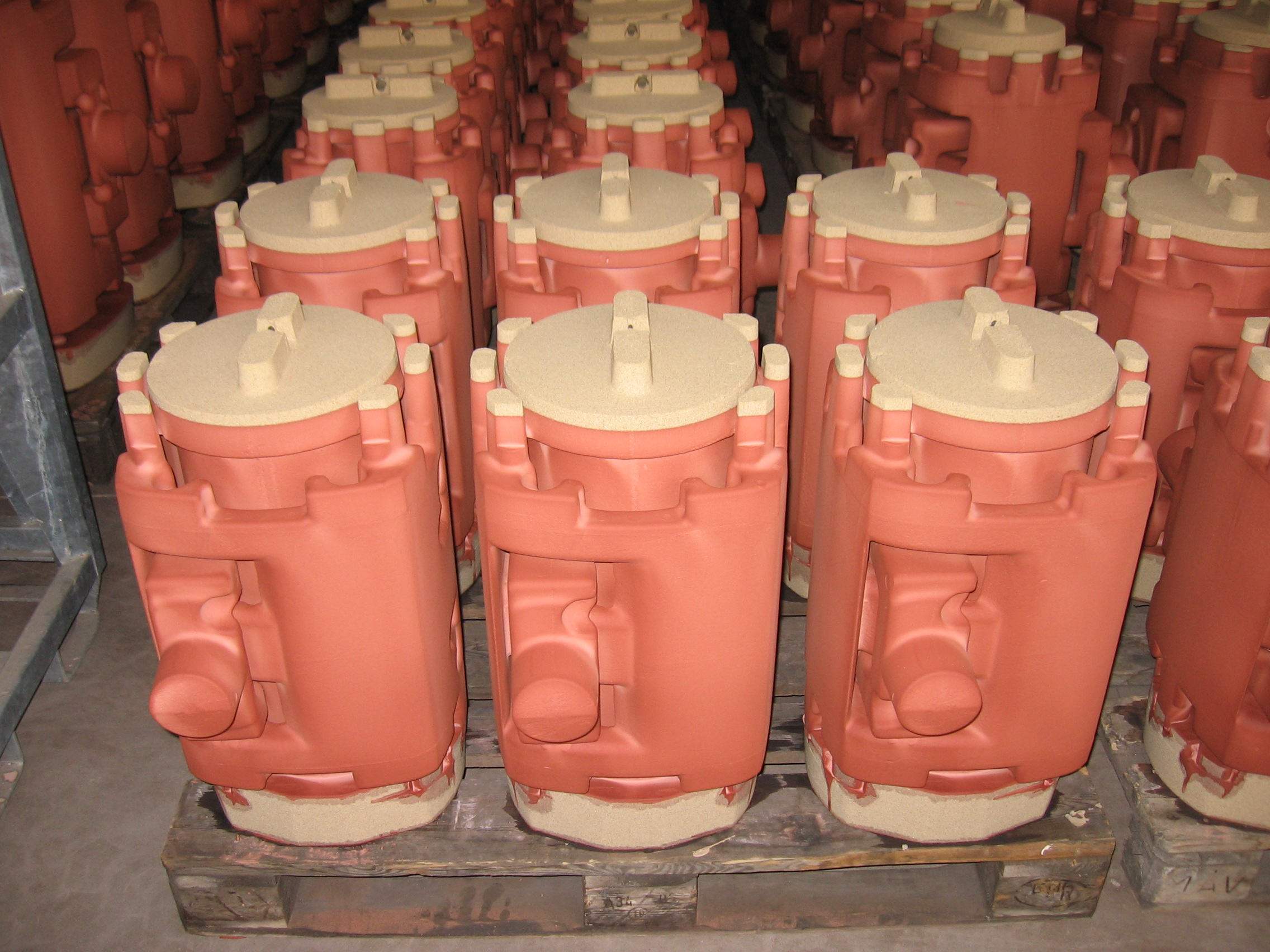
Due to the many variables involved in the casting process, it is difficult to control all the variables that can lead to a defect in the part. The best way to combat defects is to design a strategy in the core/mould manufacturing strategy that limits the influence these variables can have on the part.
⇒ LET’S CREATE A STRATEGY
1. To begin with, the foundry must monitor and control the casting temperatures and time, and the type of metal. Once the casting temperature is under control, control of other variable “processes” can be addressed.
2. Secondly, the addition of SphereOx to the system is recommended. SphereOx is manufactured by a very unique and controlled process under precise chemical specifications and with high particle size uniformity. SphereOx is a spherical shaped particle with a core composed of pure FeO, which is encapsulated by outer layers of swept Fe₂O₃ gas and a veining preventive element, Fe₃O₄.
As mentioned above, silica sand expands at an average of approximately 5%. When molten metal enters a mould, thermal expansion takes place and often causes the bond between the sand particles to fracture, causing veining.
Years ago, sand additives were introduced to soften the core to allow expansion and prevent fracture. Most of the existing additives and iron oxides on the market are angular in shape and require more resin to achieve the tensile strengths, with SphereOx this is not necessary.
⇒ THE DIFFERENCES WITH SPHERE OX
Unlike angular shaped particles, when resin is burned into spherical shaped SphereOx particles, these not only promote the free passage of harmful gases that have been generated in the metal/mould phase to escape through the mould, but also the SphereOX will absorb some of the gas generated. This is even more remarkable, when SphereOx is used in conjunction with a mostly spherical silica grain, 20-30% less resin is required to achieve proper adhesion between the sand and resin. Even with angular sand, using the SphereOx requires 10% less resin. Less resin to burn equals less harmful gases and VOCs generated. The end result is moulded parts with no pores or shiny carbon defects. Keeping resin levels to a minimum has many benefits, both economically and ecologically.
⇒ THE MALE MOULD
Mould/core dimensional stability is another critical factor for defect-free parts. In many cases foundries use high-priced zirconium sand as a replacement for silica sand when dimensional stability is critical. SphereOx has a higher specific gravity than zirconium sand (5.2 vs. 4.7), as well as a higher thermal conductivity – the result is higher cooling power without any expansion.
Therefore, many foundries use a more economical blend of SphereOx and silica sand as a substitute for zirconium sand when dimensional stability is critical. Zirconium sand is increasingly limited and overpriced at around €2,000/tn compared to the SphereOx and silica sand blend, which averages less than €200/tn.
Thermal distortion is a method of measuring the propensity of a core, in an iron or steel casting, to fracture upon melting. Thermal distortion data is evaluated (table below) on 3 different samples, and shows the undulations of each sample as well as the thermal distortion over time. At 40 seconds, the “silica sand” curve breaks down and can no longer resist thermal expansion forces (would produce a penetration), however, the male samples having a “5% SphereOx/silica sand” and the “zirconium sand” continue to respond, and allow thermal expansion and contraction, which ends in solidification. This test provides evidence that it is possible to substitute a mixture of SphereOx and silica sand for the more expensive zirconium sand, and achieve very similar results.
Historically, foundries require core tensile strengths to determine the percentage of resin needed to make a core that is strong enough for immediate handling and subsequent transport to the casting line without breakage. The core must be strong enough to resist thermal distortion under the pressures generated by the incoming molten metal.
In many cases, the casting process uses sand recovered through a mechanical sand recovery system and then a percentage of this regenerated sand is mixed with new sand at a cost saving. A mechanical sand recovery system reduces metal particles and impurities retained in the sand used, but often does not significantly reduce the retained resin. A subsequent LOI (Loss on Ignition) will indicate the percentage of resin remaining in the recovered sand. The LOI value should be added to the percentage of resin that is added from new resin. LOI values of more than 1.50% are considered high, with a higher propensity for gas related defects. Studies by many foundries using SphereOx indicate that SphereOx actually produces a GOI (Gain on Ignition) of approximately 10%, demonstrating its ability as a gas scrubber to prevent gas defects.
SphereOx has a neutral pH (7.1), making it compatible with most resin and binder systems.
⇒ THE EVIDENCE
In addition, recent studies on a massive, large section steel part provided by an EPMA (Electron Probe Micro-Analyzer) show that the SphereOx particles used in the contact sand, at elevated temperatures, penetrate the core of the part and create a much more effective barrier that prevents metal penetration. The EPMA data verifies that there is no sign of burn-in in the samples where SphereOx was used as an additive in the contact sand, however, samples where SphereOx is not used as an additive exhibit high burn-in defects. It was also observed during this study that SphereOx particles improve the chemical homogeneity of the part core, and also improve the surface finish of the part.
It is important to be consistent and control the amount (percentage) of resin and additive that is mixed with the sand when making a mould or core. Because SphereOx is spherical, has a constant size, and has no dust or impurities, it flows well and flow rates are easy to control. Traditional iron oxides and other commercially available additives are fine-grained and angular in shape. These materials do not flow easily and tend to reduce feed systems, resulting in non-uniform distribution levels from batch to batch. Non-uniform distribution causes process variations and a much higher probability of casting defects. In almost all cases when SphereOX is used to replace other additives, a decrease in binder percentage of 10-20% is observed for optimum results.
Conclusion
For almost two decades, the use of SphereOx has shown an unprecedented level of success worldwide in the prevention of casting defects, significantly reducing the cost of raw material (resin). In Spain and Portugal it is possible to buy SphereOx through our distributor EUSKATFUND, S.L.
We will always try to find the most efficient solution to any problem, in all aspects.
PROJECT AFTER PROJECT
EUSKATFUND is constantly evolving and developing. Thanks to projects like these, and the support we have received, we have managed to go a step further in the treatment and result of the materials we provide; never leaving aside one of our main values, that of being on the side of the environment whenever possible.
MORE POSTS YOU MAY BE INTERESTED IN
Properties & Applications of Ceramic Foundry Sand CERAMSAND
Ceramic sand has distinguished performance in foundry in compare with silica sand and other popularly used special sands. This article introduces the production process, the physical and chemical properties, and the application features of ceramic sand.
FUNCTIONAL CORE SHOOTER MACHINES
Adjectives that would describe the characteristics of an efficient core shooter are: versatile, practical, comfortable, fast, economical, …
THERMAL SAND RECLAMATION
Thermal reclamation has reached a point where, thanks to its innovations, it is profitable, economical and reliable.
INNOVATION R + D + I
EUSKATFUND collaborates with the technological research centres, laboratories and universities where it participates and develops projects with a high technological and environmental load.
We will tell you about some of them.