Properties & Applications of Ceramic Foundry Sand CERAMSAND
Ceramic sand has distinguished performance in foundry in compare with silica sand and other popularly used special sands. This article introduces the production process, the physical and chemical properties, and the application features of ceramic sand,
ABSTRACT
As new artificial sand, ceramic sand has been rapidly extended in foundry use in virtue of steady research and marketing for about two decades. Ceramic sand has excellent properties, including spherical shape, high refractoriness, good crush resistance, inert chemical characteristics, high reclamation yields, etc. Ceramic sand has distinguished performance in foundry in compare with silica sand and other popularly used special sands. This article introduces the production process, the physical and chemical properties, and the application features of ceramic sand, as well as its application examples in many kinds of foundry processes such as self-hardening molding, sodium silicate sand, cold box, Croning shell method, and lost foam castings. Some technical parameters of ceramic sand usage are also presented.
Has distinguished performance in foundry in compare with others
1. INTRODUCTION
eramic sand, has a visual image in figure 1, technically named as “fused ceramic sand for foundry”, is made from calcined bauxite which main content is aluminum oxide, processed by melting, blowing, sieving and blending. The production process is shown in figure 2. Operators put the calcined bauxite that contains 45%-90% aluminum oxide into the electric arc melting device. The ore melts into liquid outflow under high temperature. At the moment, the outflow is blown into fine particles by compressed air with a certain pressure. By surface tension, the spherical or spheroidal sand grains are formed with smooth surface. After cooling and sieving, the ceramic sands of different particle are graded.
From figure 1, we can see that ceramic sand has a spherical shape with very smooth surface, and has not any cracks or concave-convex. The angularity factor of ceramic sand is less than 1.1 by test.
Silica Sands
↓ Fig.1 Electron microscopic photographs of ceramic sand ↓
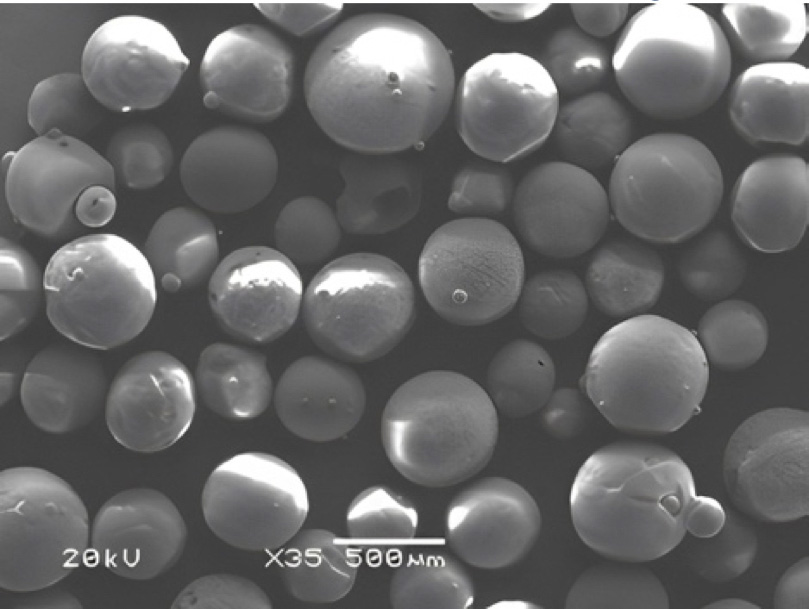
a. Low-magnification
Till now, silica sand is the most popularly used foundry sand for its appropriate foundry properties and steady availability. While it has a number of disadvantages as a base sand. It has a high thermal expansion rate which may cause expansion defects in castings, such as finning or veining and scabbing. It has a relatively low refractoriness which can cause sand burn-on, particularly with steel or heavy section iron castings. It is chemically reactive to certain alloys; for example, ferrous alloys containing manganese. The oxides of manganese and iron react with silica to form low melting point silicates, leading to serious sand burn-on defects.
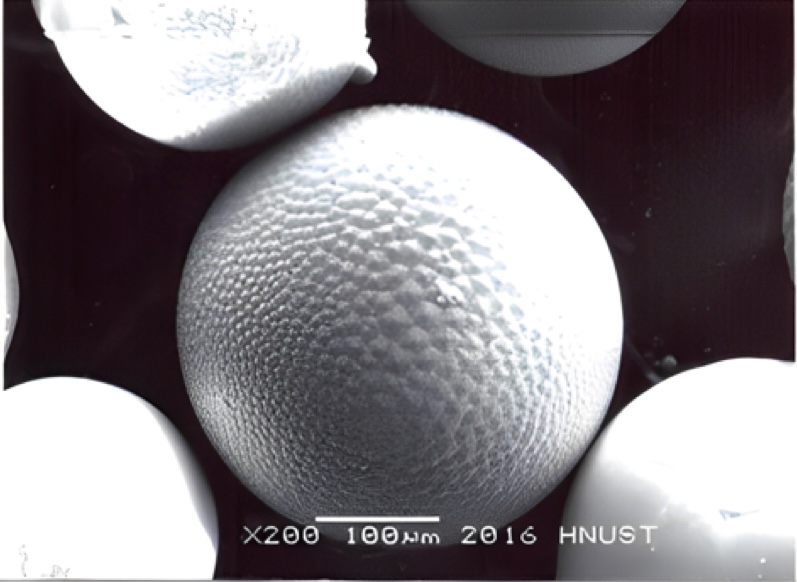
b. High-magnification
↓ Fig.2 Production diagram of ceramic sand ↓
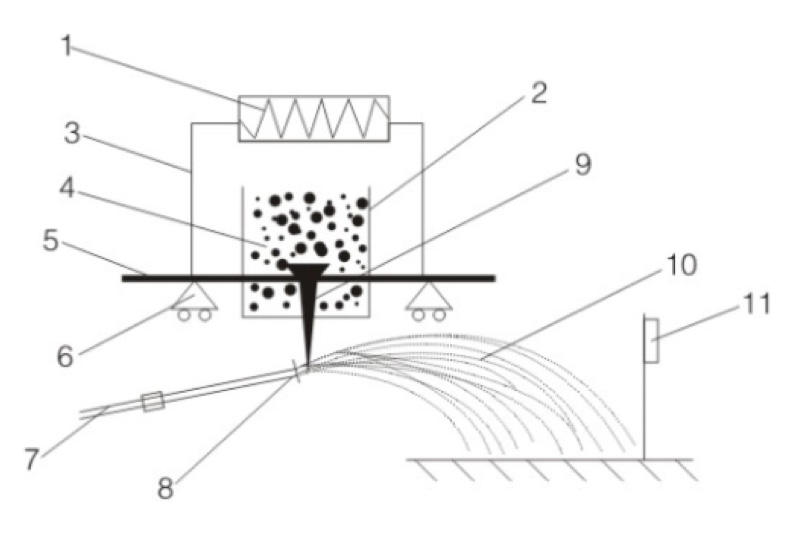
1. Transformer/ 2. Furnace body/ 3. Copper wire/ 4. Ore of bauxite/ 5. Graphite electrode/ 6. Electrode feeding device / 7. Air hose / 8. Tuyere / 9. Melted ore/ 10. Ceramic sand grains /11. Dust extraction
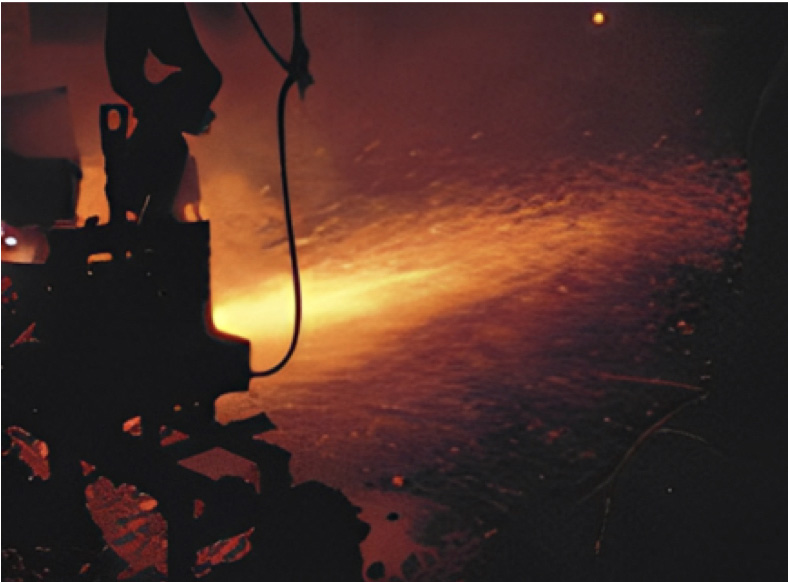
Ceramic sand, on the other hand, has much better properties than that of silica sand to gain a better performance in foundry. For its unique material and processing, it has high refractoriness, stable inert characteristics, excellent flowability, intrinsic hardness and wear resistance. And, its good spherical grain shape forms bonds efficiently, requires reduced binder levels. Also, in this consideration, ceramic sand has much better overall advantages compare with other special sands, including zircon and chromite.
The use of ceramic sand provides an opportunity for foundries to reduce casting costs and promote casting quality, as well as to build an environment-friendly production system.
2. Physical and Chemical Properties of Ceramic sand
The main chemical components of ceramic sand are aluminum dioxide and silica dioxide. After melting and recrystallization, ceramic sand has a mineralogical composition of mullite, corundum and trace amorphous substances. Its refractoriness is generally more than 1800℃ and is an aluminum-silicon refractory material of high hardness. The colors of ceramic sand include taupe, black brown. Table 1 shows the main physical and chemical properties of ceramic sand.
Table 1 Physical and chemical properties of ceramic sand (typical)
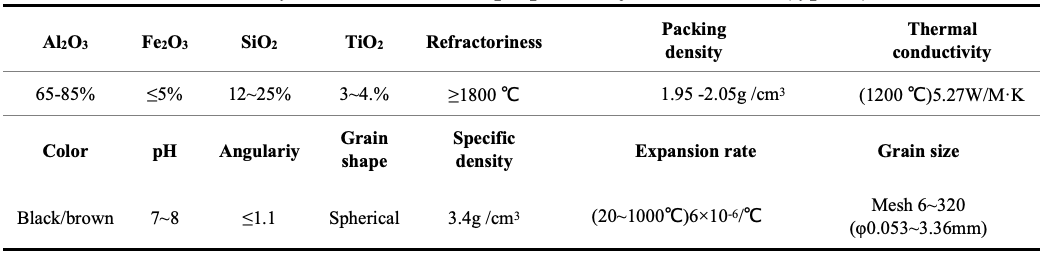
3. Characteristics of ceramic sand
As a special foundry sand, the ceramic sand has the following characteristics:
(1) The thermal expansion rate of ceramic sand is very low, similar to that of zircon sand. Using ceramic sand to make moulds and cores, veins and other expansion defects of castings may be eliminated.
(2) Ceramic sand has good flowability, and easy to fill in because of its spherical shape. The moulds and cores are of high permeability and easy to shakeout after casting.
(3) By using ceramic sand, 30-50% of the binder consumption can be saved, to obtain castings with good finish and substantial structure economically.
(4) Ceramic sand is a neutral and inert material, so it can be used in acid and alkali binders systems, also adapt to various alloys.
(5) Ceramic sand has good recycling performance. It can be easily reclaimed by many methods.
(6) Ceramic sand has high refractoriness and good stability. It is especially suitable for the production of complex sand cores and steel castings.
(7) It has wide particle size distribution, which can be combined and mixed arbitrarily to meet specific needs of customers.
4. Applications of ceramic sand in foundry
Now, ceramic sand has been commonly used in cast iron, cast steel, stainless steel and non-ferrous castings with kinds of foundry technologies, such as furan no-bake, Croning shell method, cold box, phenolic alkali no-bake, ester cured sodium silicate process and lost foam castings. Below is a pie chart of ceramic sand usage based on recent data.
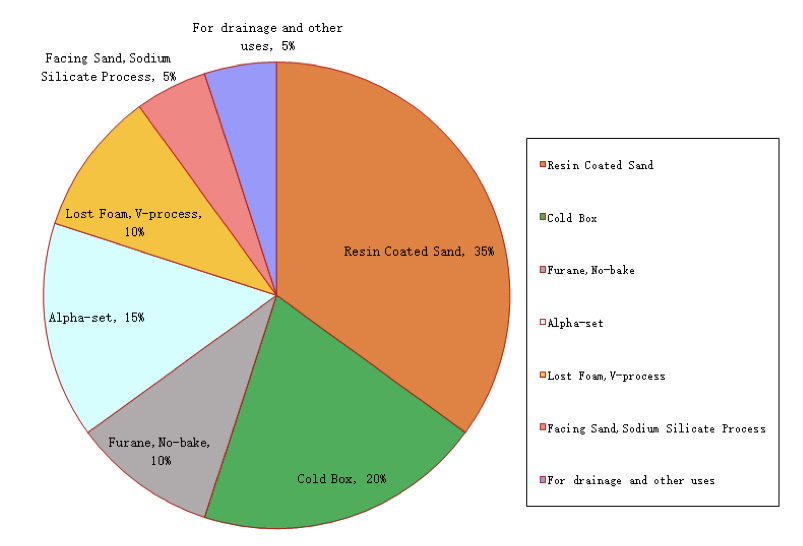
← Fig.3 Pie chart of ceramic sand applications
4.1 Furan No-bake Process
For furan bonded ceramic sand, its hardening rate is much higher than silica sand, and when adding the same amount of resin, the strength is remarkably improved.
To test the tensile strength of ceramic sand and Dalin silica sand, add 1.2% furan resin of the weight of sands and catalyst by 40% weight of furan resin respectively, the curing time is arranged in 1, 2, 3, 4, 5 and 24 hours, then test the tensile strength at the arranged time (with “8” type test pieces), the test result is shown in Table 2.
Table 2 Tensile strength of ceramic sand and Dalin silica sand
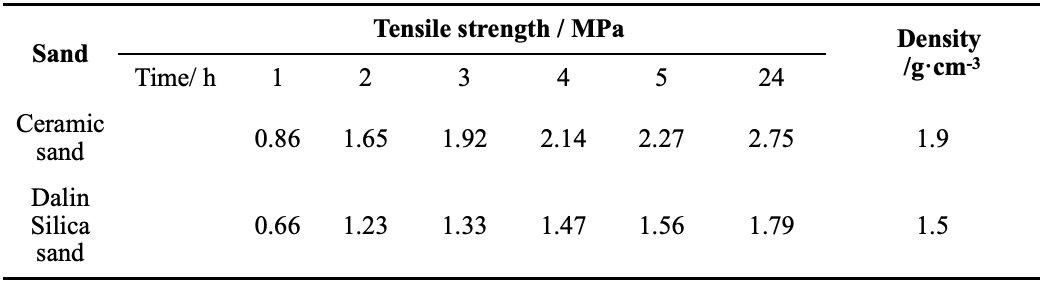
It shows that the tensile strength after 24 hours of ceramic sand is over 50% higher than that of silica sand. It has been proved that the use of ceramic sand can not only reduce the amount of resin, save costs, improve production efficiency, but also greatly reduce the casting defects such as porosity.
4.2 Resin Coated Sand Molding and Core Making, Shell Process
4.2 Resin Coated Sand Molding and Core Making, Shell Process
Taking advantages of ceramic sand, people can make high quality resin coated sand, which has exceptional properties such as high refractoriness, low thermal expansion, easy to shakeout, high strength, and less gas evolution. For particularly complex cores (see fig.4a and 4b), resin coated ceramic sand has good flow-ability, which can solve the problem of being not fully formed.
↓ Fig.4 Resin coated sand cores and castings ↓
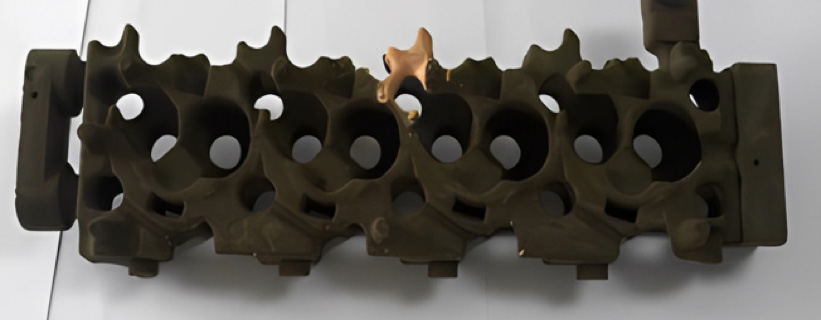
a. Water jacket core of cylinder head
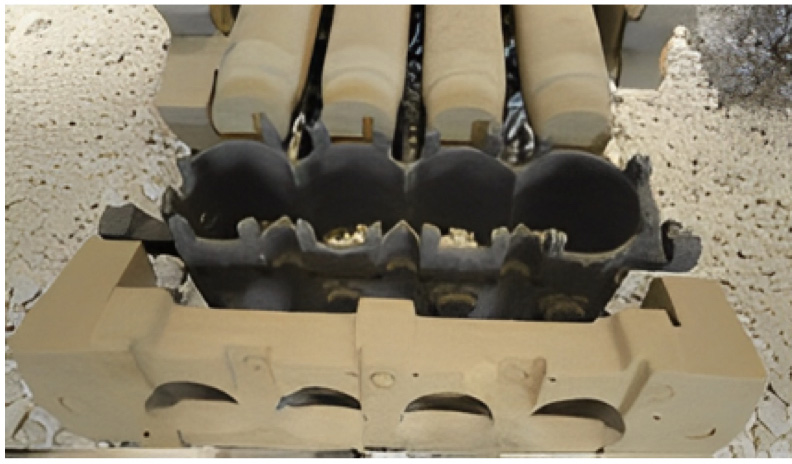
c. Cores assembly
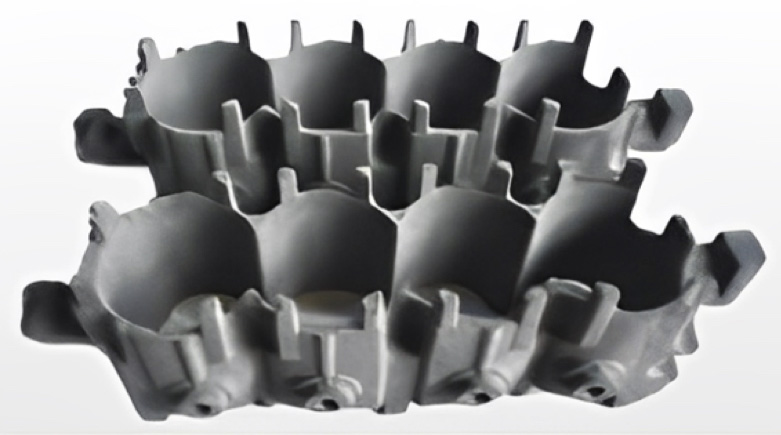
b. Water jacket core of cylinder block
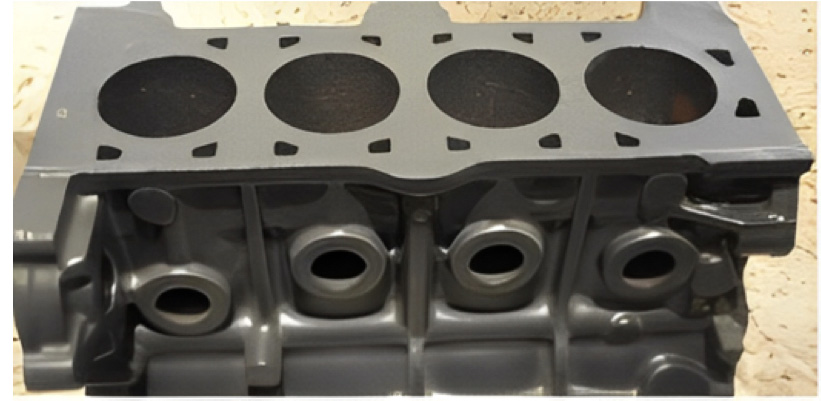
d. Cylinder block
The shell process of the ceramic sand (see fig.5) is of high production efficiency. The casting dimensional accuracy and the castings finish are exceptional. The used sand is easy to recycle, which greatly reduces the emission of solid wastes. The environmental benefits of this process are also remarkable.
It can be predicted that, as a new green manufacturing technology, the shell mold casting process using ceramic sand will become a new foundry technology widely used.
↓ Fig.5 Shell molds and castings ↓
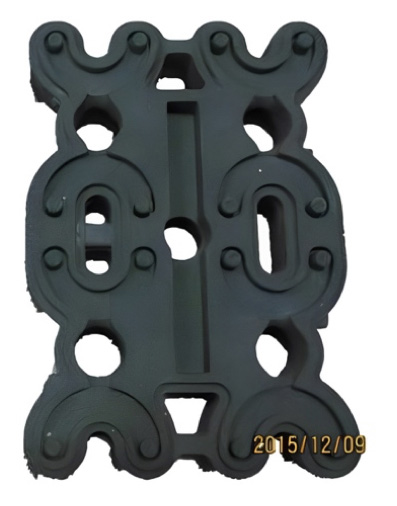
a. Single core piece for shell method
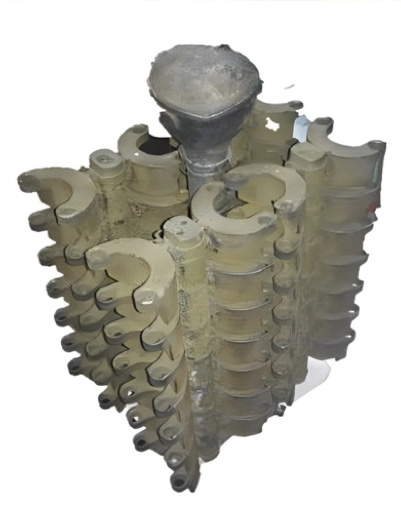
b. Castings clutch with gating system made by shell method
4.3 Alkaline-phenolic Resin (Alpha-set), Molding and Core Making
It’s well known that the pour temperature of cast steel is rather high, the use of the ceramic sand can fully take the advantages of the alkaline-phenolic resin. The sand consumption of casting can be reduced to 30-50kg per ton. The binder consumption is reduced by 30-50%, with the improvement of casting surface quality, the amount of sand shakeout and casting cleaning work can be reduced more than 60%. It can significantly improve the casting quality, reduce the rejection rate and production cost. It also reduces the emission of waste gas, sand and dust, improves the work environment, prevents silicosis, and achieves the goal of green production.Fig.6 shows cores and castings of stainless high pressure valves made by Alpha-set process using ceramic sand.
↓ Fig.6 Alpha-set process ceramic sand cores and a casting. ↓
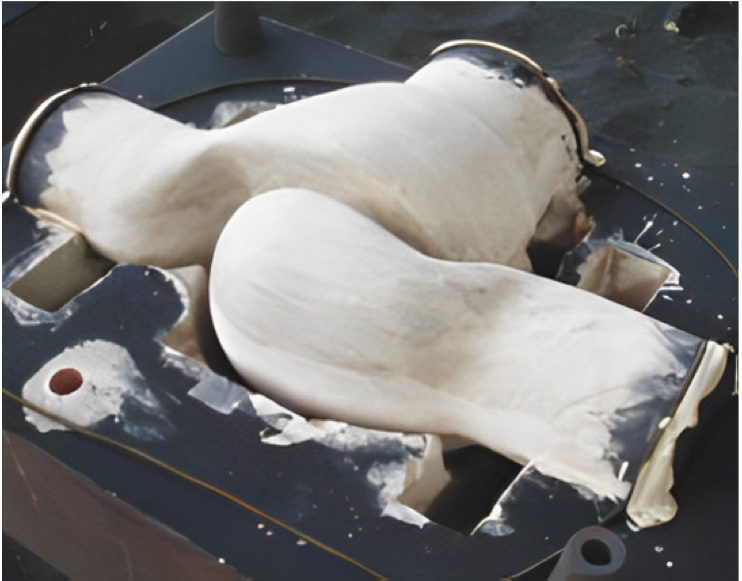
a. Moulds and cores
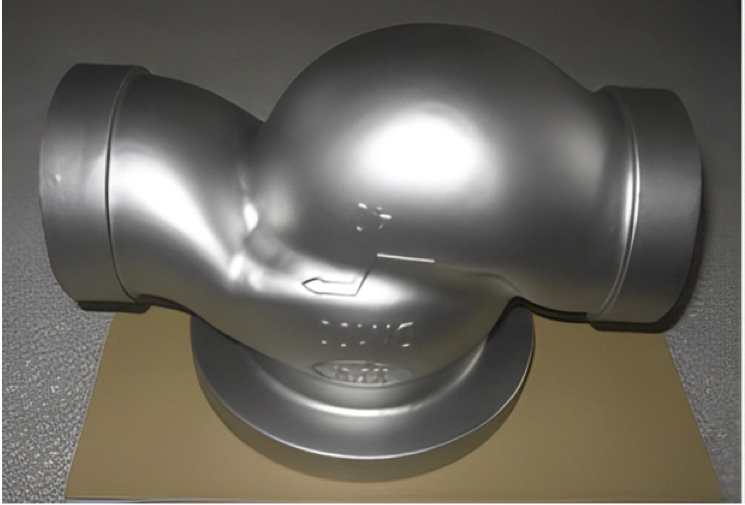
b. High pressure valve casting
Table 3 shows strength performances of ceramic sand Dalin silica sand using alkaline phenolic resin. We can find that the tensile strength after 24 hours is as high than that of silica sand by 31%,while the binder level of ceramic sand is less than silica sand by 40%,and the gas evolution of sand may has a reduction of 32%.In practice,using ceramic sand,foundry can save the binder consumption by 45-55%.
Table 3 Tensile strength of ceramic sand and Dalin standard sand by Alpha-set process.
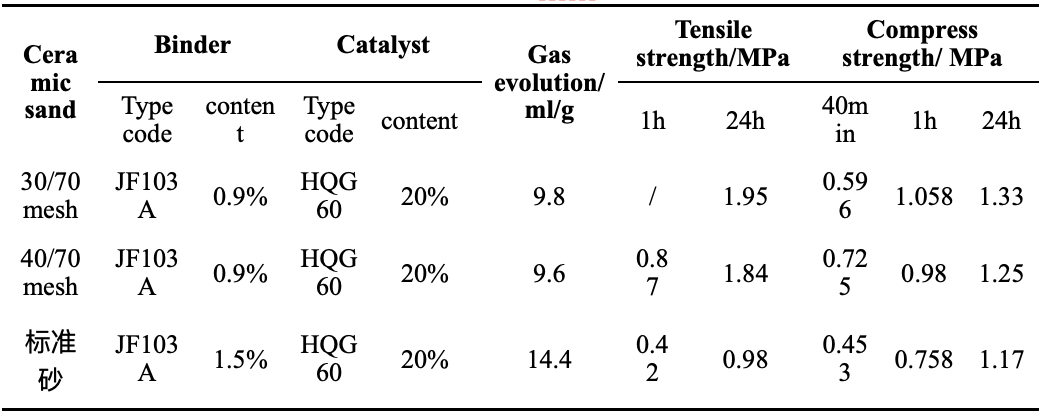
4.4 Sodium-silicate Bonded Sand
For heavy section cast steel, it generally has much higher static liquid pressure onto moulds and cores during a relatively longer pouring time. The mechanical, thermal and chemical reactions between metal and moulds may be violent. These can lead severe metal penetration and sand burn-on, especially at the parts of intersection of castings. This takes a lot of works for foundries to handle where castings may have poor finish, and the working places may be environmentally horrible. In some circumstances, bad working conditions exposes workers to the danger of silicosis.
To solve the problems of metal penetration and sand burn-on, we have had a site production trial. Add 3%~4.5% of silicate to ceramic sand, then thoroughly mixed, put the mixed sand to the parts marked “A” on moulds shown in Fig7, then put sodium silicate bonded silica sand to complete molding. After coating and pouring, we obtained castings without metal penetration and sand burn-on. It demonstrates the anti-penetration properties of ceramic sand.
Figure 8 shows the local (wall intersections, core, etc.) of large cast steel parts where ceramic sand facing sand used. These parts are prone to sintering, penetration and burn-on. Using ceramic facing sand to fulfill the long straight holes of the supporting roller, results show that this can not only reduce the likelihood of metal penetration, but also eliminate the possibility of casting crack due to thermal stress caused by poor thermal deformability by using silica sand.
↓ Fig.7 Filling position of ceramic sand ↓
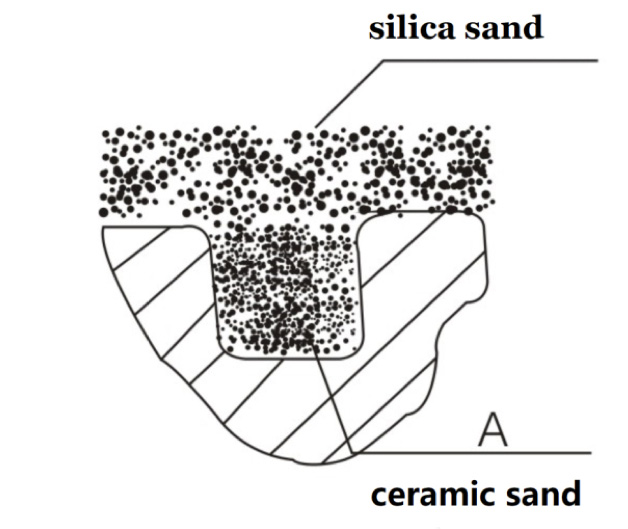
↓ Fig.8 Sodium silicate molding and core-making (supporting roller steel casting) ↓
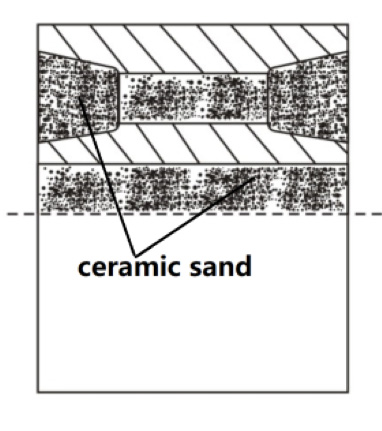
a. Filling position of ceramic sand
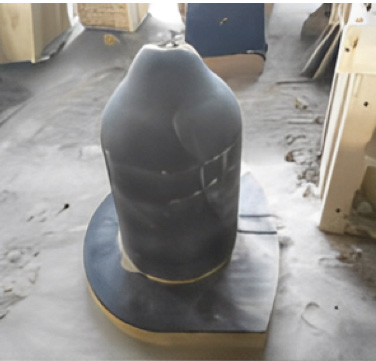
b. Ceramic sand using at core surface
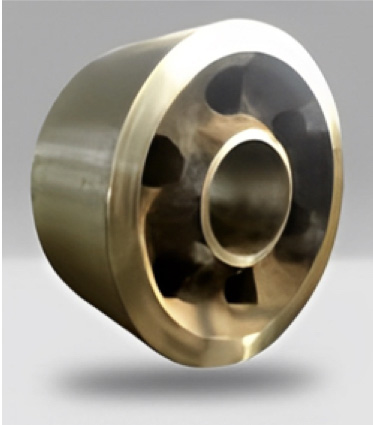
c. Supporting roller (cast steel)
At present, besides the using ceramic sand as facing sand separately, its mixture with chromite in the sodium silicate sand can also take the advantages of ceramic sand and chromite overall . In addition to using CO2 hardened sodium silicate sand, ceramic sand also has significant advantages in the ester hardened process. Table 4 compares the tensile strength of ceramic sand and silica sand by ester hardening sodium silicate process.
Table 4 Tensile strength of ceramic sand and Dalin silica sand by ester-hardening sodium silicate.
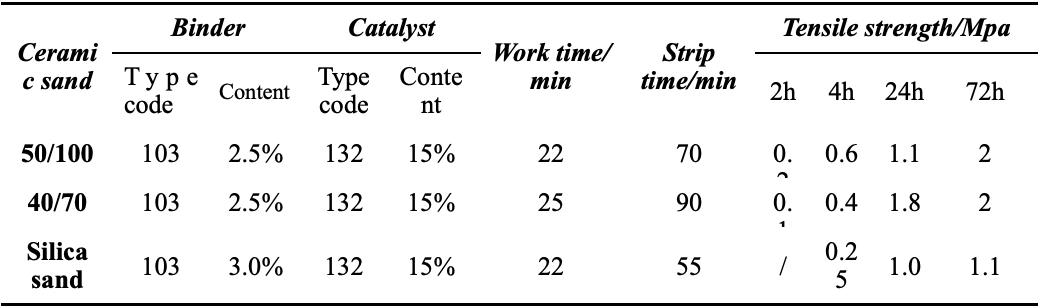
4.5 Lost Foam Process and V-process
For lost foam process and v-process, people use ceramic sand as backing sand, the rate of qualified products increases remarkably. The total cost decreases, the sand consumption of castings is only 1-2kg per ton. And, the working environment is obviously improved because of its round shape, good flow-ability, strong durability, high thermal conductivity, lower dust, etc.
Figure 9c illustrates the lost foam process and a casting of an engine cylinder block. When use silica sand, those slender holes can hardly fulfill properly, may cause iron-sand sintering and serious penetration that, cannot be cleaned. Using ceramic sand, the above problems can be eliminated. Ceramic sand, has good spherical shape, provides good permeability, good flowability excellent filling performance. It also has low crush rate during molding and reclamation, so that the cost of castings will be declined while the production yield may be as high as 97%.
↓ Fig.9 Lost foam molding and castings ↓
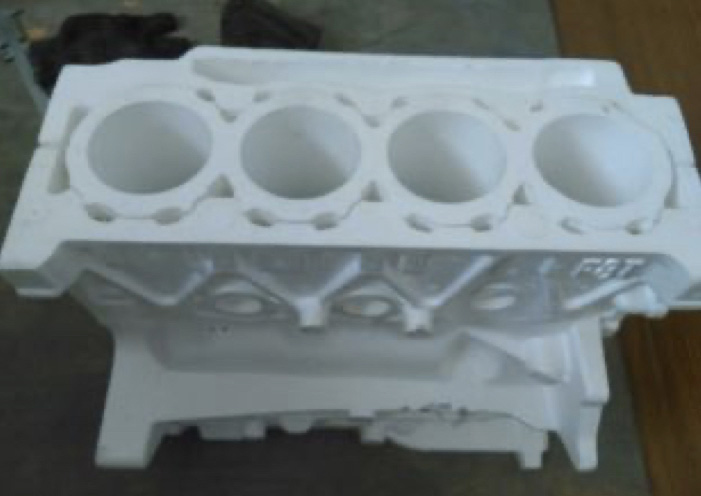
a. Foam pattern
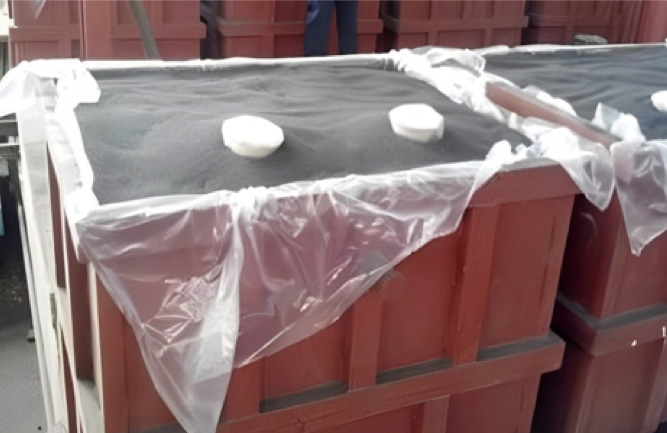
b. Molding by using ceramic sand
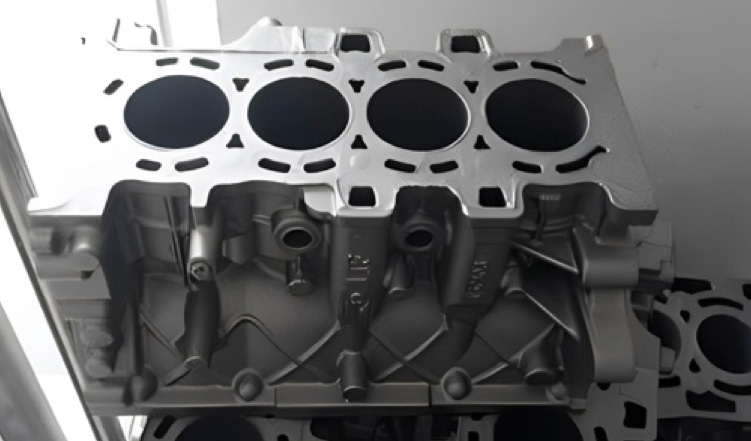
c. A cylinder block made by lost foam process
Conclusions
(1) In no-bake processes (including Furan and phenolic alkali no-bake), use ceramic sand can improve sand strength significantly, can save binder level by over 30%, so as to decline gas evolution, gain reclamation yields as high as to 98%, and eliminate solid emission remarkably.
(2) Using ceramic sand as base sand in resin coated sand cores and shell method, the flowability of RCS is excellent, the expansion rate and gas evolution is rather low, so that reduces the defects such as gas holes and veins of castings.
(3) The use of ceramic sand in sodium silicate systems reduces binder consumption apparently, enhance the properties to shake-out, avoid penetration and sand burn-on, and can cut down castings cost.
(4) In application of lost foam casting production, use ceramic sand can improve flowability, then improve sand filling, improve permeability and so on. Due to the high strength and low crushing rate of ceramic sand, the reclamation yields of the sand is high and the cost is low.
With the rapid development of foundry industry, to meet social environmental protection requirements, more and more manufacturers will choose ceramic sand as base sand partly or overall. Ceramic sand, a new foundry material in the 21st century, will play a more significant role in the new era of sustainable development and green manufacturing
We will always try to find the most efficient solution to any problem, in all aspects.
PROJECT AFTER PROJECT
EUSKATFUND is constantly evolving and developing. Thanks to projects like these, and the support we have received, we have managed to go a step further in the treatment and result of the materials we provide; never leaving aside one of our main values, that of being on the side of the environment whenever possible.
MORE POSTS YOU MAY BE INTERESTED IN
Sphere Ox, a feasible solution.
Veining, burns, penetrations and pinholes are common defects in castings and the daily struggle of foundries to control them. We tell you the solution.
FUNCTIONAL CORE SHOOTER MACHINES
Adjectives that would describe the characteristics of an efficient core shooter are: versatile, practical, comfortable, fast, economical, …
THERMAL SAND RECLAMATION
Thermal reclamation has reached a point where, thanks to its innovations, it is profitable, economical and reliable.
INNOVATION R + D + I
EUSKATFUND collaborates with the technological research centres, laboratories and universities where it participates and develops projects with a high technological and environmental load.
We will tell you about some of them.