Propriétés et applications du sable de fonderie céramique CERAMSAND
Le sable céramique CERAMSAND présente des performances extraordinaires par rapport au sable de silice et à d’autres sables spéciaux couramment utilisés. Cet article présente le processus de production, les propriétés physiques et chimiques et les caractéristiques d’application du sable céramique CERAMSAND.
RÉSUMÉ
En tant que nouveau sable artificiel, le sable céramique CERAMSAND s’est rapidement répandu dans les fonderies grâce à des recherches et un marketing constants depuis environ deux décennies. Le sable céramique CERAMSAND présente d’excellentes propriétés, notamment une forme sphérique, une réfractarité élevée, une bonne résistance à l’écrasement, des caractéristiques chimiques inertes, des rendements de récupération élevés, etc. Le sable céramique CERAMSAND présente des performances extraordinaires par rapport au sable de silice et à d’autres sables spéciaux couramment utilisés. Cet article présente le processus de production, les propriétés physiques et chimiques et les caractéristiques d’application du sable céramique CERAMSAND, ainsi que ses exemples d’application dans de nombreux types de procédés de coulée, tels que le moulage NO BAKE, le sable de silicate de sodium, Cold Box, la méthode de moulage en coque de Croning et les moulages en mousse perdue. Certains paramètres techniques de l’utilisation du sable céramique CERAMSAND sont également présentés.
Il présente des performances exceptionnelles par rapport à d’autres
1. INTRODUCTION
Le sable céramique, représenté sur la figure 1, et techniquement appelé « sable céramique fondu CERAMSAND pour fonderie », est composé de bauxite calcinée dont le contenu principal est l’oxyde d’aluminium, traité par fusion, soufflage, tamisage et mélange. Le processus de production est illustré à la figure 2. Les opérateurs placent de la bauxite calcinée contenant 45 à 90 % d’oxyde d’aluminium dans le dispositif de fusion à arc électrique. Le minerai est fondu pour former un écoulement liquide à haute température. À ce moment-là, le flux de sortie est soufflé en fines particules par de l’air comprimé à une certaine pression. La tension superficielle produit des grains de sable sphériques ou sphéroïdaux à surface lisse. Après refroidissement et tamisage, les sables céramiques de différentes particules sont classés.
Sur la figure 1, on peut voir que le sable céramique a une forme sphérique avec une surface très lisse et ne présente pas de fissures ni de formes concaves ou convexes. Le facteur d’angularité du sable céramique est inférieur à 1,1 selon les tests.
Sables Siliceux
↓ Fig.1 Fotografías microscópicas electrónicas de arena cerámica ↓
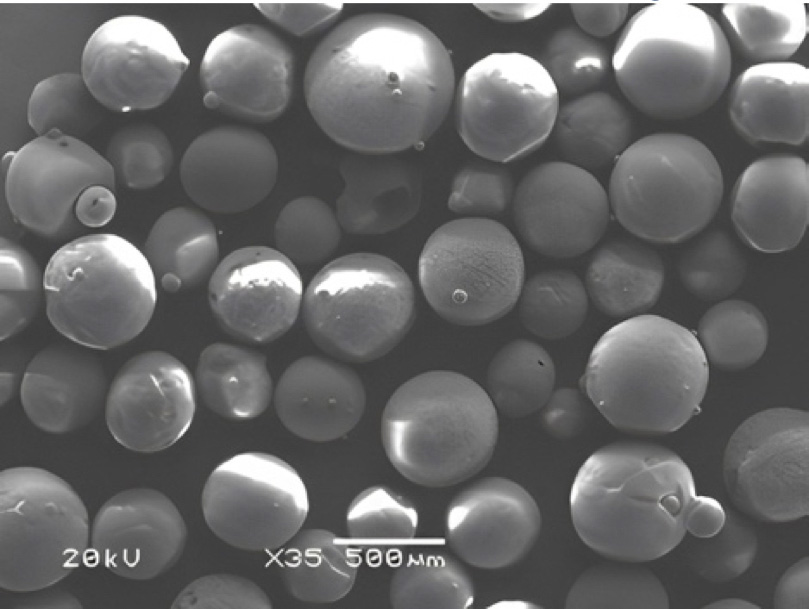
a. Faible grossissement
À ce jour, le sable de silice est le sable de fonderie le plus utilisé en raison de ses propriétés appropriées et de sa disponibilité abondante. Bien qu’il présente un certain nombre d’inconvénients en tant que sable de base. Il présente un taux de dilatation thermique élevé qui peut provoquer des défauts de dilatation dans les pièces moulées, tels que des veines et des écailles. Il présente une réfractarité relativement faible qui peut provoquer des calcinations de sable, en particulier dans les pièces moulées en acier ou en fonte de section lourde. Il est chimiquement réactif à certains alliages ; par exemple, les alliages ferreux contenant du manganèse. Oxydes demanganèseetferréagissent avec la silice pour former Silicates à bas point de fusion, qui provoquent de graves défauts de calcination dans le sable.
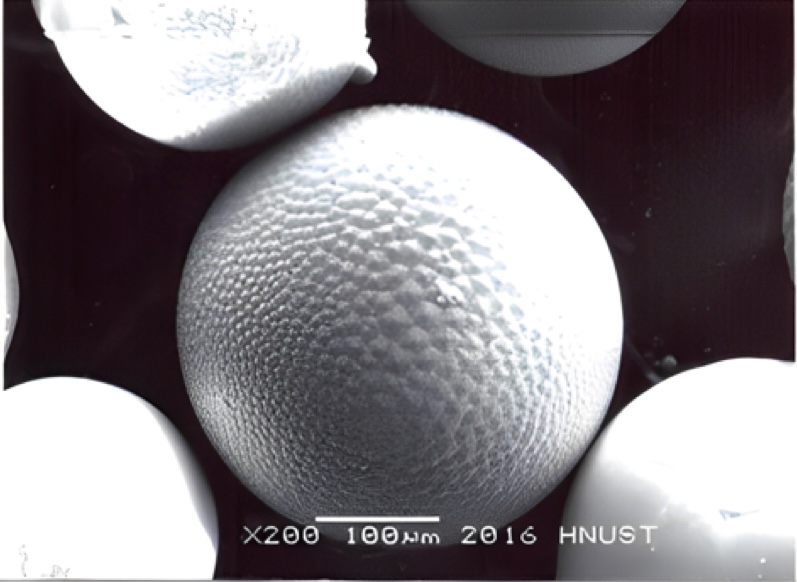
b. Fort grossissement
↓ Fig. 2 Diagramme de productionion de sable céramique CERAMSAND ↓
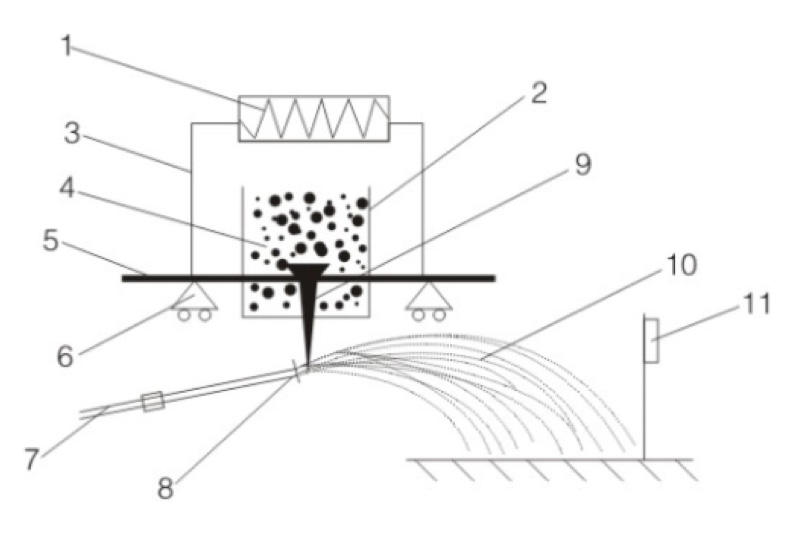
1. Transformateur / 2. Corps du four / 3. Fil de cuivre / 4. Minerai de bauxite / 5. Électrode en graphite / 6. Dispositif d’alimentation d’électrodes / 7. Tuyau d’air / 8. Buse / 9. Minéral fondu / 10. CERAMSAND / 11 grains de sable céramique. Extraction de poussière.
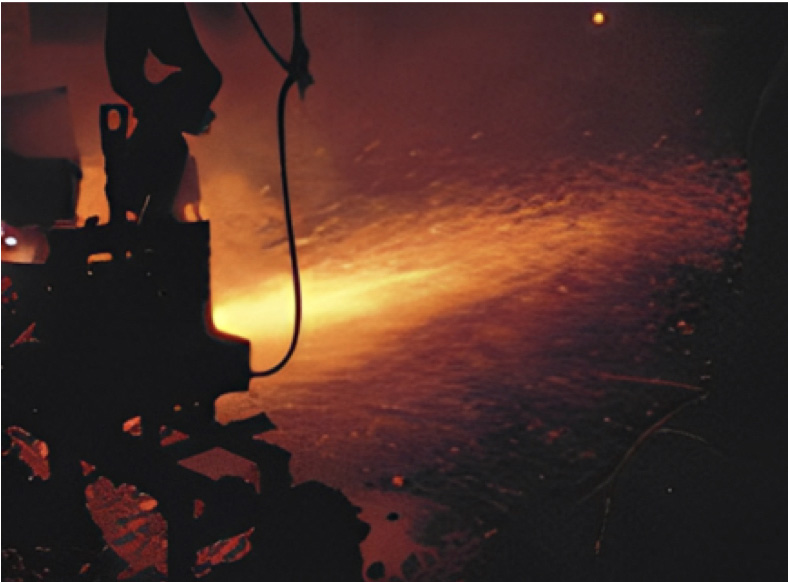
Le sable céramique CERAMSAND, quant à lui, possède de bien meilleures propriétés que le sable de silice pour obtenir un mieux performance de coulée. En raison de sa composition et de son traitement uniques,a une réfractarité élevée,est inerte et écurie, a excellente fluidité, haut pureté, il est résistant à l’usure et présente des grains sphériques.Le forme ronde des liaisons efficacement et nécessite des niveaux réduits d’aglomerant. En plus, en ce sens, le sable céramique CERAMSAND présente de bien meilleurs avantages globaux encomparaison avec d’autres sables spéciaux,y comprissable de zirconium et le chromite.
L’utilisation du sable cermica CÉRAMSAND fournit un chance pour les fonderies afin de réduire les coûts le fonderie et promouvoir la qualité. Donc comme pour construire un Système de production respectueux de l’environnement.
2. Propriétés physiques et chimiques du sable céramique CERAMSAND
Les principaux composants chimiques du sable céramique CERAMSAND sont le dioxyde d’aluminium et le dioxyde de silice. Après fusion et recristallisation, le sable céramique a une composition minéralogique de mullite, de corindon et de traces de substances amorphes. Sa réfractarité est supérieure à 1800℃ et c’est un matériau réfractaire à base d’alumine-silicium de haute dureté. Les couleurs du sable en céramique comprennent le taupe et le noir. Le tableau 1 présente les principales propriétés physiques et chimiques du sable céramique CERAMSAND.
Tableau 1 Propriétés physiques et chimiques du sable céramique CERAMSAND (typiques)
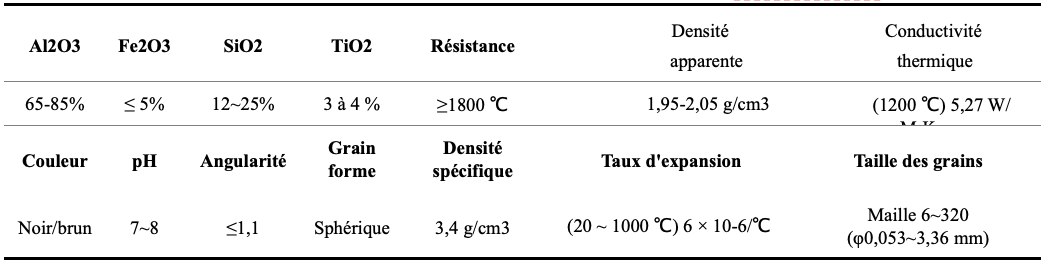
3. Caractéristiques du sable céramique CERAMSAND
Comme le sable de fonderie spécial, le sable céramique CERAMSAND a les éléments suivants caractéristiques:
(1) La dilatation thermique du sable céramique est très faible, similaire à celle du sable de zirconium. En utilisant du sable céramique pour fabriquer des moules et des noyaux, les veines, les croûtes et autres défauts de dilatation peuvent probablement être éliminés des pièces moulées.
(2) Le sable céramique présente une bonne fluidité et est facile à enduire grâce à sa forme sphérique. Les moules et les noyaux ont une perméabilité élevée et sont faciles à dessabler après la coulée.
(3) En utilisant du sable céramique, vous pouvez économiser entre 30 et 50 % de la consommation de liant, obtenant pièces moulées avec une bonne finitionet réduire les coûts.
(4) Le sable céramique est un matériau neutre et inerte, il peut donc être utilisé dans des systèmes avec des liants acides et alcalins, et peut également être utilisé avec divers alliages.
(5) Le sable céramique a de bonnes performances de recyclage et peut être facilement récupéré par de nombreuses méthodes.
(6) Le sable céramique présente une réfractarité élevée et une bonne stabilité. Il est particulièrement adapté à la production de noyaux de sable complexes et de pièces moulées en acier et en fer de grandes sections.
(7) Il présente une large distribution granulométrique qui peut être combinée et mélangée arbitrairement pour répondre aux besoins spécifiques des clients.
4. Applications du sable céramique CERAMSAND en fonderie
Actuellement, le sable céramique CERAMSAND est utilisé généralement dans fonderies de fer, acier, acier inoxydable et non ferreux avec différents types declasseurs, pas de cuisson furanique, méthode Croning, Boîte froide, Alcaline phénolique sans cuisson, processus Sans cuisson de silicate de sodium durci avec ester et fonderie de mousse perdue. Suivant,a est affiché graphique circulaire d’utilisation de le sable céramique basé sur des données récentes:
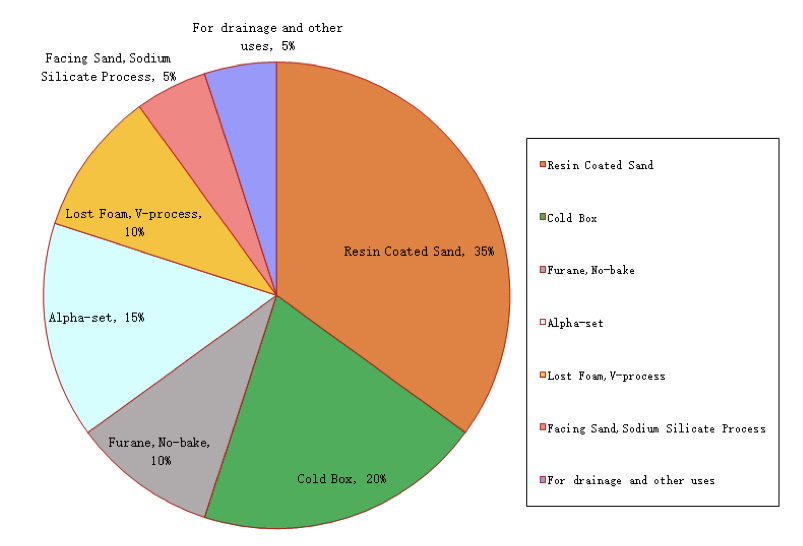
← Fig. 3 Diagramme circulaire des applications du sable céramique CERAMSAND
4.1 Procédé furanique sans cuisson
Dans le cas du sable céramique aggloméré avec de la résine furanique, les résistances mécaniques à froid sont bien supérieures à celles obtenues avec du sable siliceux. En ajoutant la même quantité de résine, la résistance s’améliore considérablement..
Pour tester la résistance à la traction du sable céramique et du sable de silice, une résine furanique de base est utilisée en ajoutant respectivement 1,2 % du poids du sable et 40 % du catalyseur au poids des résines. Les tubes à essai sont cassés à 1, 2, 3, 4, 5 et 24 heures. Pour chaque fraction de temps, 8 tubes à essai sont cassés. Le résultat du test est présenté dans le tableau 2.
Tableau 2. Résistance à la traction du sable céramique CERAMSAND et du sable de silice Dalin
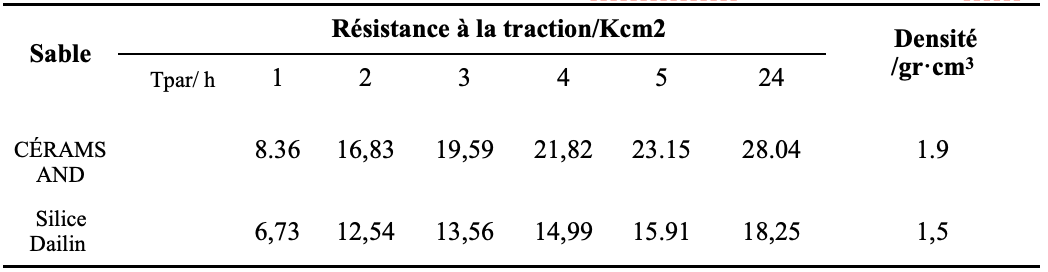
Il est démontré que la résistance à la traction après 24 heures, avec le sable céramique CERAMSAND, est plus de 50 % supérieure à celle du sable de silice Dalin. Il a été prouvé que l’utilisation de sable céramique peut non seulement réduire la quantité de résine, économiser les coûts, améliorer l’efficacité de la production, mais également réduire considérablement les défauts de coulée tels que la porosité.
4.2 Fabrication de noyaux par procédés COLD BOX et SHELL MOLDING
En tirant parti des avantages du sable céramique CERAMSAND, des sables pré-enrobés de haute qualité peuvent être fabriqués avec des propriétés exceptionnelles telles qu’une réfractarité élevée, une faible dilatation thermique, un dessablage facile, une résistance mécanique élevée et des émissions de gaz réduites. Pour les hommes particulièrement complexes.(voir fig. 4a et 4b), le sable céramique pré-enduit a une excellente fluidité, ce qui peut résoudre le problème d’avoir unformé.
↓ Fig. 4 Pièces moulées et noyaux en sable pré-revêtus ↓
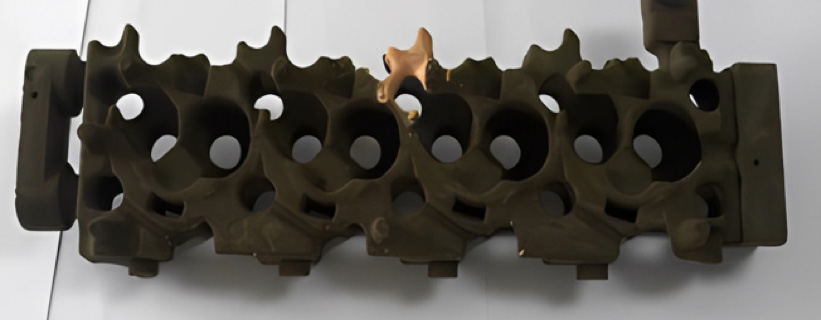
a. Noyau chemise d’eau de la culasse
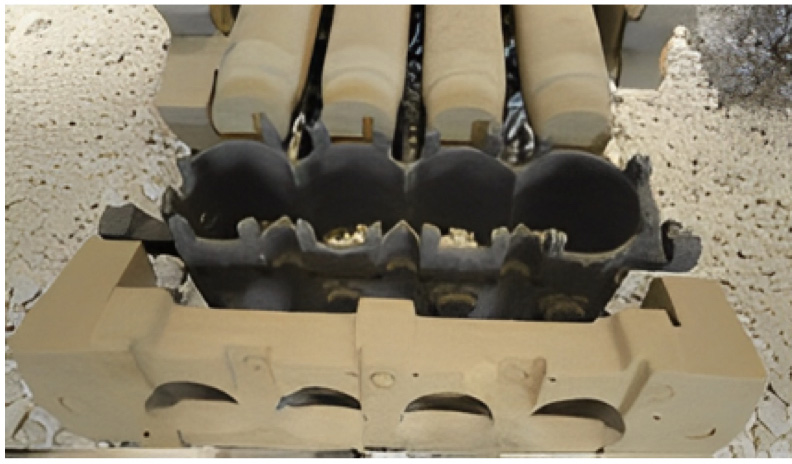
c. Ensemble des noyaux
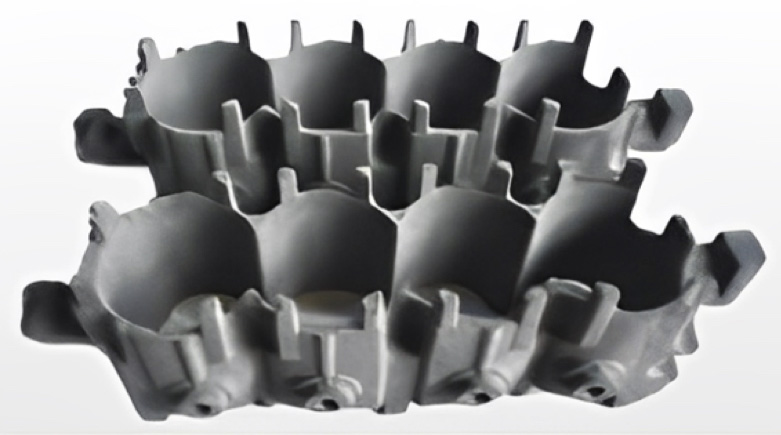
b. Noyau chemise d´eau du bloc-cylindres.
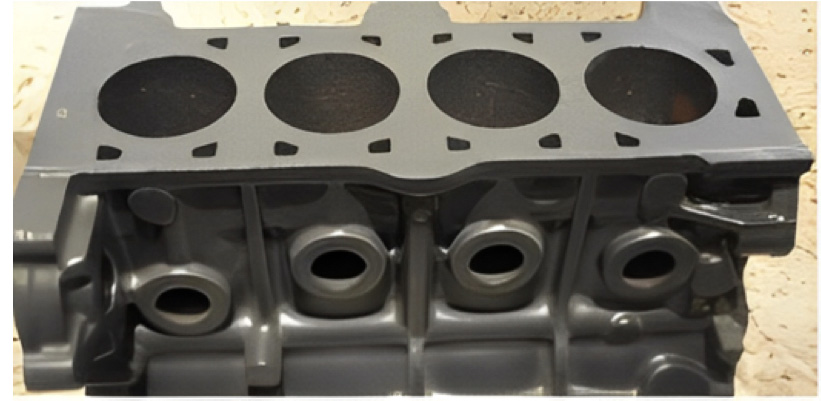
d. Bloc-cylindres
Le procédé de moulage de coquille avec du sable céramique (voir fig. 5). Le processus de moulage est très efficace, la précision dimensionnelle et la finition des pièces sont exceptionnelles et le sable utilisé est facile à recycler, ce qui réduit considérablement les émissions de déchets solides. Les avantages environnementaux de ce procédé sont également notables.
Il est prévu qu’en tant que nouvelle technologie de fabrication verte, le procédé de moulage en coquille de sable céramique deviendra une nouvelle technologie de moulage largement utilisée.
↓ Fig. 5 Moules et pièces moulées en Shell ↓
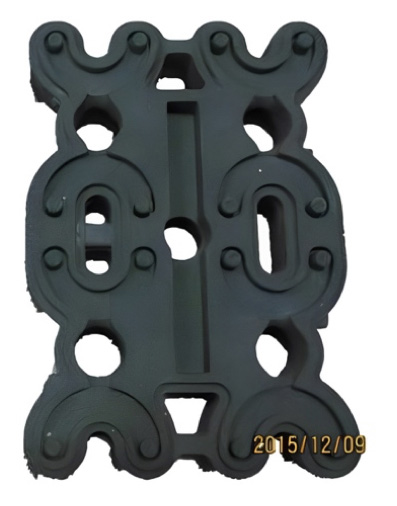
a. Coulée monocoque pour la méthode Shell
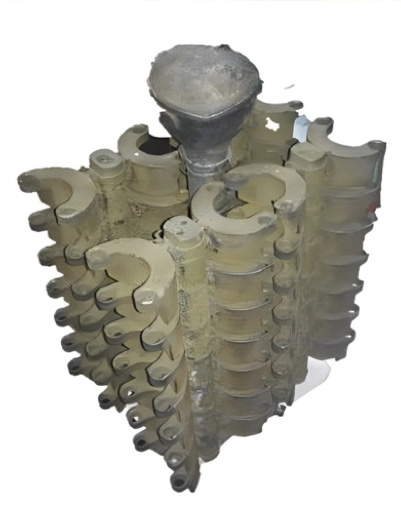
b. Moulages en grappes de coquillage avec le système Shell
4.3 Résine phénolique alcaline, moulage et fabrication de noyaux
Il est bien connu que la température de coulée de l’acier en fusion est assez élevée, donc l’utilisation de sable céramique nous permet de profiter pleinement des avantages de la résine phénolique alcaline. La consommation de sable de fonderie peut être réduite à 30-50 kg par tonne. La consommation de liant est réduite de 30 à 50 %. En améliorant la qualité de surface de la pièce moulée, la quantité de travail de récupération de sable et de nettoyage de la pièce moulée peut être réduite de plus de 60 %. Il peut améliorer considérablement la qualité de la coulée, réduire le taux de rejet et les coûts de production. Il réduit également les émissions de gaz résiduaires, de sable et de poussière, améliore l’environnement de travail, prévient la silicose et atteint l’objectif de production verte. La figure 6 montre des noyaux de soupapes haute pression en acier inoxydable et des pièces moulées fabriquées par le procédé phénolique alcalin utilisant du sable céramique CERAMSAND.
↓ Fig.6 Noyaux de sable céramique avec procédé phénolique alcalin et fondu. ↓
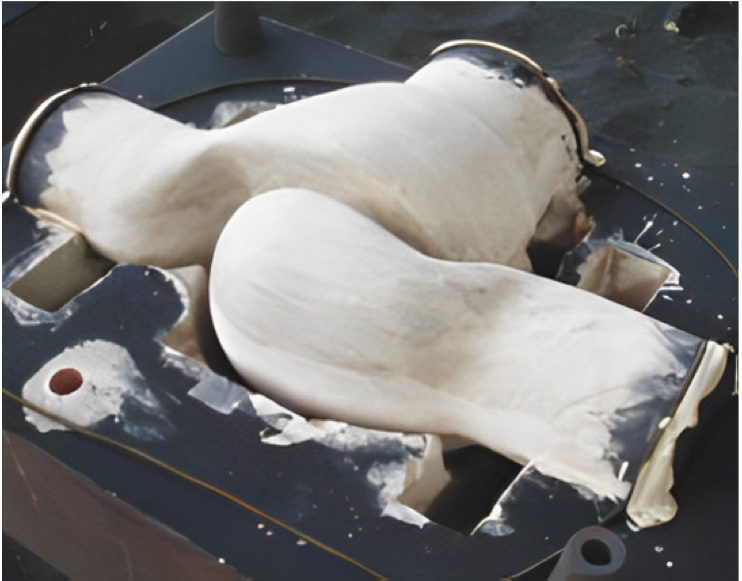
a. Moules et noyaux
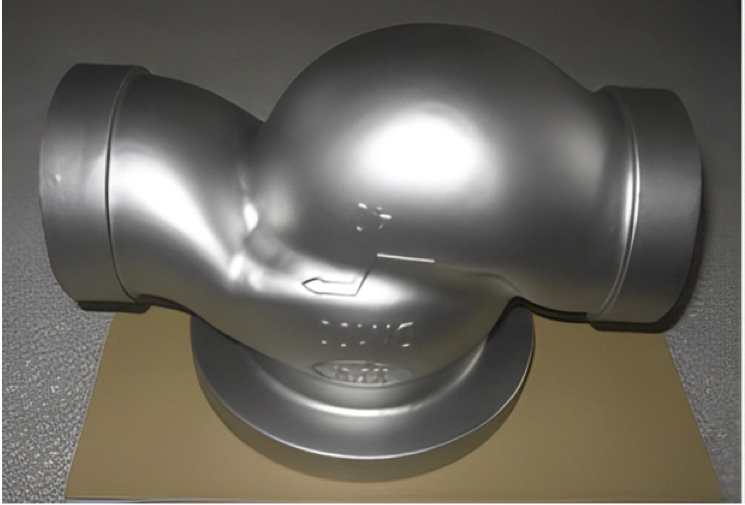
b. Fonderie de soupape haute pression
Le tableau 3 montre les performances de résistance du sable céramique par rapport au sable de silice Dailin utilisant une résine phénolique alcaline. Nous pouvons constater que la résistance à la traction après 24 heures est 31 % supérieure à celle du sable de silice, tandis que le niveau de liant du sable céramique est 40 % inférieur à celui du sable de silice, et le dégagement de gaz du sable peut être réduit de 32 %. En pratique, en utilisant du sable céramique, les fonderies peuvent économiser de 45 à 55 % la consommation de résine.
Tableau 3 Résistance à la traction du sable céramique et de la silice Dalin avec le procédé phénolique alcalin
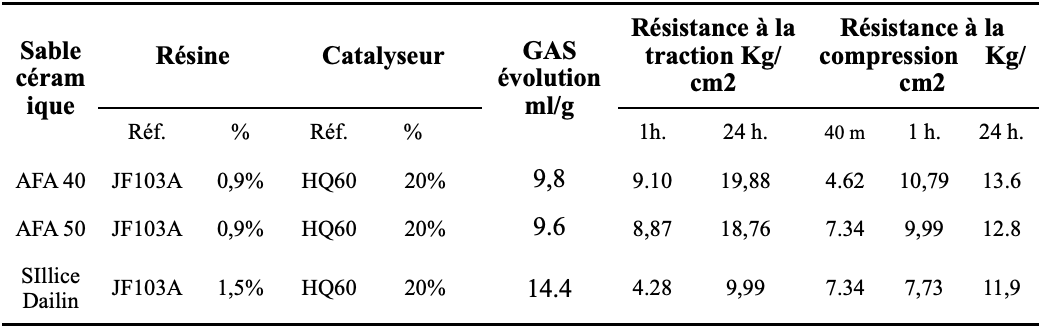
4.4 Sable aggloméré avec silicate de sodium
Dans le cas d’acier moulé à section lourde, la pression statique de la masse fondue sur les moules et les noyaux est généralement beaucoup plus élevée sur une durée de coulée relativement plus longue. Les réactions mécaniques, thermiques et chimiques entre le métal et les moules peuvent être violentes. Ces derniers peuvent provoquer de graves pénétrations de métal et des brûlures de sable, en particulier aux intersections des pièces moulées. Cela nécessite beaucoup de travail dans les fonderies pour ébavurer les pièces moulées qui peuvent avoir une finition médiocre, et les ateliers d’ébavurage sont soumis à des conditions environnementales de travail horribles. Dans certaines circonstances, de mauvaises conditions de travail exposent les travailleurs au risque de silicose.
Pour répondre aux problèmes de pénétration du métal et de calcination du sable, nous avons mené un essai de production sur site. Nous ajoutons entre 3% et 4,5% de silicate au sable céramique, mélangeons bien et attaquons le sable mélangé dans les parties marquées « A ». Dans les moules représentés sur la Fig. 7, nous ajoutons ensuite une charge de sable de silice agglomérée avec du silicate. Après peinture et coulage, nous avons obtenu des pièces moulées sans pénétrations de sable ni calcinations. Ceci démontre les propriétés anti-pénétration du sable céramique CERAMSAND.
La figure 8 montre le détail (intersections des parois, du noyau, etc.) de grandes pièces en acier moulé où le sable céramique CERAMSAND est utilisé comme sable de contact. Ces zones sont sujettes au frittage, à la pénétration et à la calcination. Nous utilisons du sable de contact céramique pour remplir les trous profonds et droits du support du rouleau. Les résultats montrent que cela peut non seulement réduire la pénétration du métal, mais également éliminer la possibilité de fissuration due à la contrainte thermique causée par une mauvaise déformabilité thermique en utilisant du sable de silice.
↓ Fig. 7 Position de remplissage du sable céramique ↓
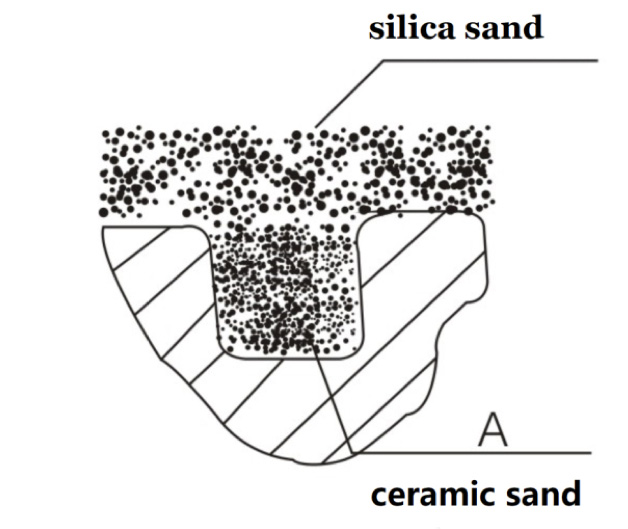
↓ Fig.8 Moulageet la fabrication du noyau avec silicate de sodium (Support de rouleau. moulage d’acier) ↓
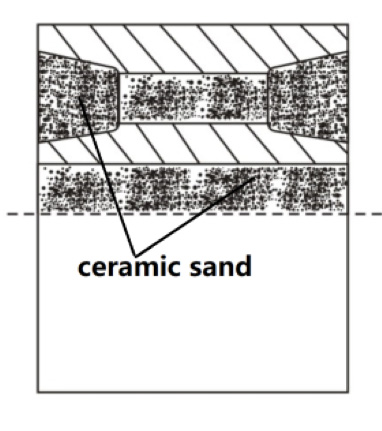
a. Position de remplissage du sable céramique
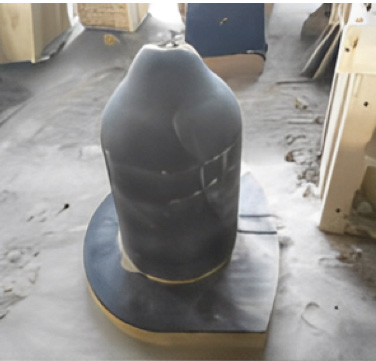
b. Du sable céramique est utilisé sur la surface du noyau.
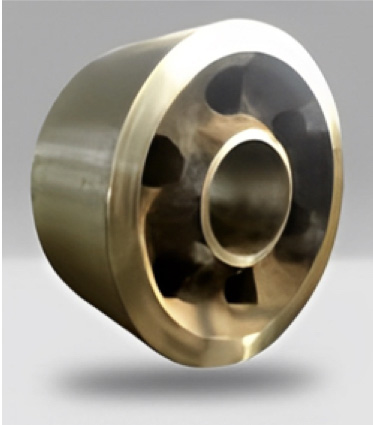
c. Rouleau de support (acier moulé)
Actuellement, en plus d’utiliser le sable céramique CERAMSAND comme sable de contact, son mélange avec de la chromite peut également profiter des avantages du sable céramique et de la chromite en général. En plus de l’utilisation de silicate de sodium durci au CO2, le sable céramique présente également des avantages significatifs dans le processus de durcissement de l’ester. Le tableau 4 compare la résistance à la traction du sable céramique et du sable de silice en utilisant le procédé de durcissement à l’ester de silicate de sodium.
Tableau 4 Résistance à la traction du sable céramique et du sable de silice Dalin aggloméré avec du silicate de sodium et un durcissement à l’ester
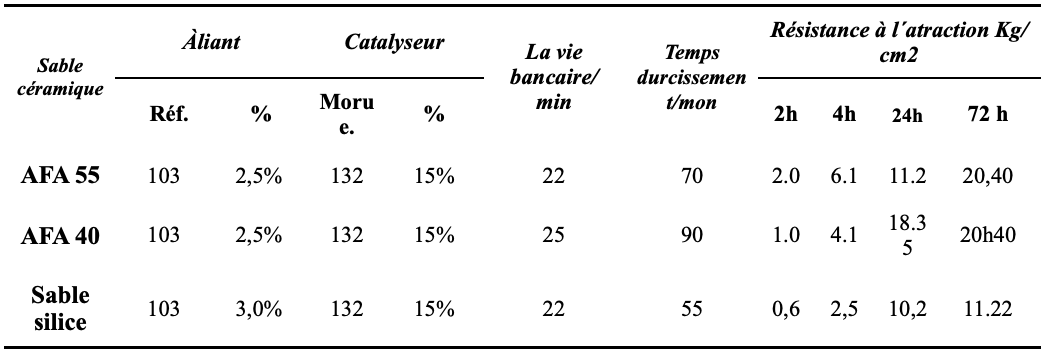
4.5 Procédé de mousse perdue et procédé en V
Pour le procédé de mousse perdue et le procédé V, les fonderies utilisent du sable céramique comme sable de support. Grâce à CERAMSAND, le taux de pièces rejetées diminue considérablement. Le coût total diminue. La consommation de sable des pièces moulées n’est que de 1 à 2 kg par tonne, et l’environnement de travail est évidemment amélioré grâce à sa forme ronde, sa bonne fluidité, sa grande durabilité, sa conductivité thermique élevée, moins de poussière, etc.
Figure 9 (c)illustre le processus Mousse perdueet un moule d’un bloc moteur. Lors de l’utilisation d’autres sables, ces trous profonds de petit diamètre sont difficiles à remplir et à compacter correctement, ce qui entraîne de graves problèmes de frittage et de pénétration difficiles à nettoyer et à récupérer. En utilisant le sable céramique CERAMSAND, ces problèmes peuvent être éliminés. Le sable céramique CERAMSAND a une forme sphérique, offre une bonne perméabilité, a une bonne fluidité et une bonne compactabilité. Le taux de casse du CERAMSAND lors du moulage et de la récupération est très faible, de sorte que le rejet des pièces est très faible et l’efficacité de la production peut atteindre 97 %.
↓ Fig.9 Moulage et fonderie de mousse perdue ↓
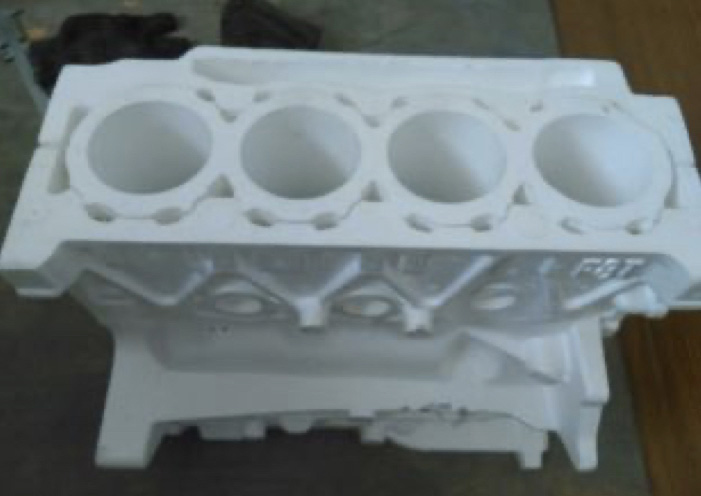
a. Modèle en mousse
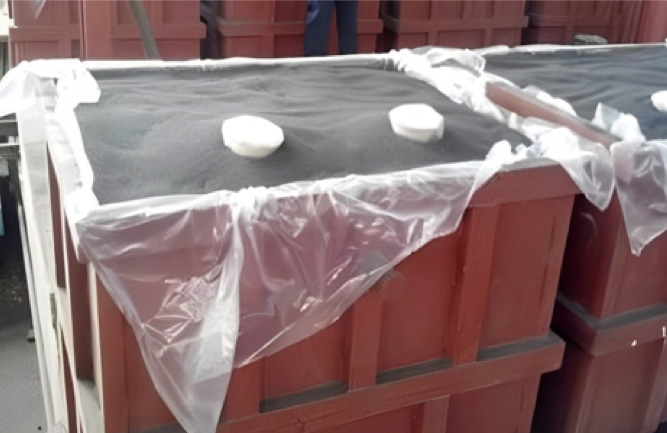
b. Moulage avec du sable céramique
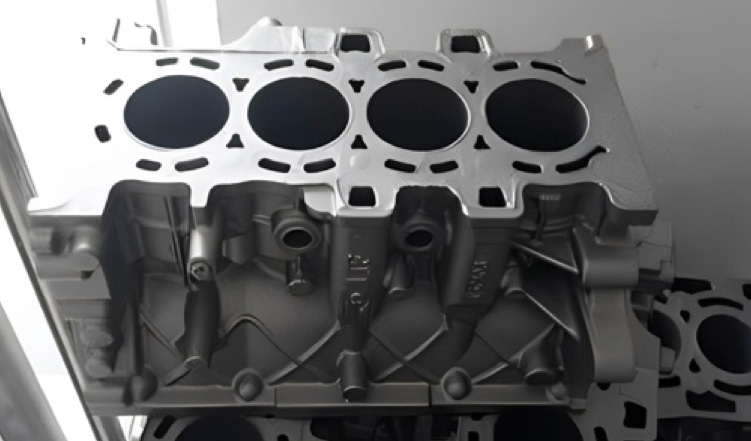
c. Un bloc-cylindres fabriqué par le procédé Lost Foam
Conclusions
(1) Dans les processus SANS CUISSON (compris systèmes alcalins furaniques et phénoliques) et l’utilisation du sable céramique CERAMSAND peut améliorer considérablement la résistance du sable aggloméré et peut sauver le pourcentage du liant de plus de 30 %, en baissele évolution de gaz et obtenir des taux de recuperation jusqu’à 98%, éliminer notamment déversement dans des décharges.
(2) En utilisant le sable céramique CERAMSAND comme sable de base dans les noyaux de sable enrobés et dans la méthode de moulage en Shell molding, la fluidité du RCS est excellente, le taux d’expansion et le dégagement de gaz sont assez faibles, réduisant ainsi les défauts de gaz tels que les piqûres et les veines dans les pièces moulées.
(3) L’utilisation du sable céramiques CERAMSAND, dans les systèmes de silicate de sodium, réduit la consommation d’aglomerant s’améliore lles propriétés pour l’enlèvement du sable, évitez le pénétrations et le calcinations, et peut réduire le coût des pièces moulées.
(4) Dans la production de moulage en mousse perdue, l’utilisation du sable céramique améliore la fluidité, le compactage du sable, la perméabilité, etc. En raison de la résistance élevée et du faible taux de rupture du sable céramique CERAMSAND, les performances de récupération du sable sont élevées et le coût est faible.
Avec le développement rapide de l’industrie de la fonderie, afin de répondre aux exigences de protection de l’environnement, de plus en plus de fabricants choisiront le sable céramique CERAMSAND comme sable de base, en partie ou en totalité. Le sable céramique, un nouveau matériau de moulage au 21e siècle, jouera un rôle plus important dans la nouvelle ère du développement durable et de la fabrication verte.
Chez EUSKATFUND, nous sommes à votre disposition pour répondre à vos questions et demandes.
Pour les problèmes, il y a des solutions ; nous nous efforcerons toujours de trouver la plus efficace à tous égards.
PROJET APRÈS PROJET
EUSKATFUND est en constante évolution et développement. Grâce à des projets comme ceux-ci et au soutien que nous avons reçu, nous avons réussi à aller plus loin dans le traitement et le résultat des matériaux que nous fournissons, sans jamais laisser de côté l’une de nos principales valeurs, celle d’être du côté de l’environnement chaque fois que c’est possible.
PLUS D’ARTICLES QUI PEUVENT VOUS INTÉRESSER
Accord de distribution entre euskatfund et Capital Refractories
Depuis Euskatfund, nous sommes fiers de montrer nos progrès et, avec eux, ceux qui nous aident à nous améliorer ; c’est pourquoi nous avons conclu cet accord avec Capital Refractories.
Certification Environnementale.
Soucieux de toujours offrir la meilleure qualité à nos clients, nous avons obtenu le certificat environnemental ISO 14001:2015 et le certificat de qualité ISO 9001:2015.
Nous avons agrandi un nouveau pavillon
Euskatfund ouvre un nouveau pavillon pour la fabrication de manches et de mazarottes.