Propiedades y aplicaciones de la arena cerámica de fundición CERAMSAND
La arena cerámica CERAMSAND tiene un rendimiento extraordinario en comparación con la arena de sílice y otras arenas especiales de uso común. Este artículo presenta el proceso de producción, las propiedades físicas y químicas y las características de aplicación de la arena cerámica CERAMSAND.
SUMARIO
Como nueva arena artificial, la arena cerámica CERAMSAND se ha extendido rápidamente en el uso de la fundición en virtud de una investigación y comercialización constantes durante aproximadamente dos décadas. La arena cerámica CERAMSAND tiene excelentes propiedades, incluida la forma esférica, alta refractariedad, buena resistencia al aplastamiento, características químicas inertes, altos rendimientos de recuperación, etc. La arena cerámica CERAMSAND tiene un rendimiento extraordinario en comparación con la arena de sílice y otras arenas especiales de uso común. Este artículo presenta el proceso de producción, las propiedades físicas y químicas y las características de aplicación de la arena cerámica CERAMSAND, así como sus ejemplos de aplicación en muchos tipos de procesos de fundición, como el moldeo NO BAKE, la arena de silicato de sodio, la Caja Fría, el método Shell Molding de Croning y las fundiciones de Lost Foam. También se presentan algunos parámetros técnicos del uso de la arena cerámica CERAMSAND.
Tiene un rendimiento extraordinario en comparación con otras
1. INTRODUCCIÓN
La arena cerámica, que se muestra en la figura 1, y que técnicamente se denomina “arena cerámica fundida para fundición CERAMSAND”, está hecha de bauxita calcinada cuyo contenido principal es óxido de aluminio, procesada por fusión, soplado, tamizado y mezclado. El proceso de producción se muestra en la figura 2. Los operadores colocan la bauxita calcinada que contiene entre un 45% y un 90% de óxido de aluminio en el dispositivo de fusión por arco eléctrico. El mineral se funde en un flujo de salida líquido a alta temperatura. En ese momento, el flujo de salida se sopla en partículas finas mediante aire comprimido con una cierta presión. Por tensión superficial, se forman los granos de arena esféricos o esferoidales con una superficie lisa. Después de enfriar y tamizar, se clasifican las arenas cerámicas de diferentes partículas.
En la figura 1 se puede observar que la arena cerámica tiene forma esférica con una superficie muy lisa y no presenta grietas ni cóncavos ni convexos. El factor de angularidad de la arena cerámica es inferior a 1,1 según las pruebas.
Arena de sílice
↓ Fig.1 Fotografías microscópicas electrónicas de arena cerámica ↓
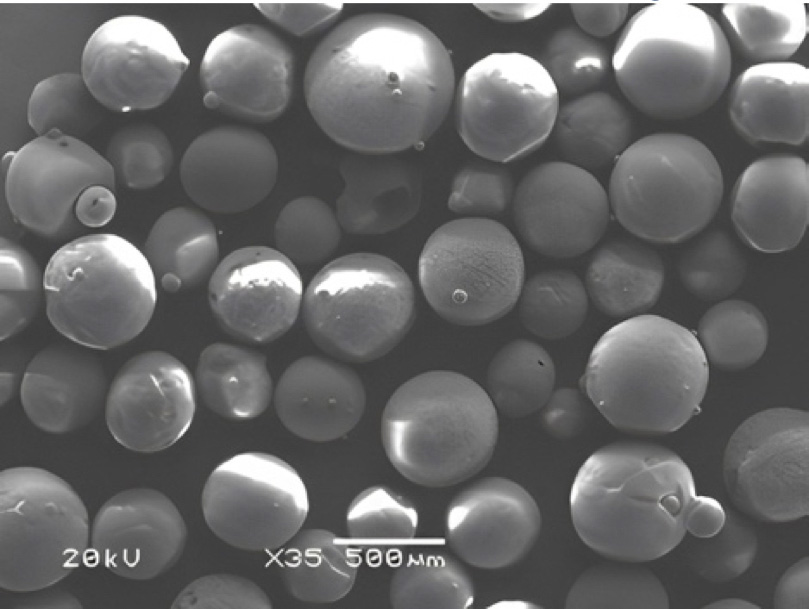
a. Bajo aumento
Hasta ahora, la arena de sílice es la arena de fundición más utilizada por sus propiedades adecuadas y su abundante disponibilidad. Si bien tiene una serie de desventajas como arena base. Tiene una alta tasa de expansión térmica que puede causar defectos de expansión en las piezas fundidas, como veining o vetas y costras. Tiene una refractariedad relativamente baja que puede causar calcinaciones de arena, particularmente en piezas fundidas de acero o de hierro de sección pesada. Es químicamente reactivo a ciertas aleaciones; por ejemplo, aleaciones ferrosas que contienen manganeso. Los óxidos de manganeso y hierro reaccionan con la sílice para formar Silicatos de bajo punto de fusión, que provocan graves defectos de calcinación de la arena.
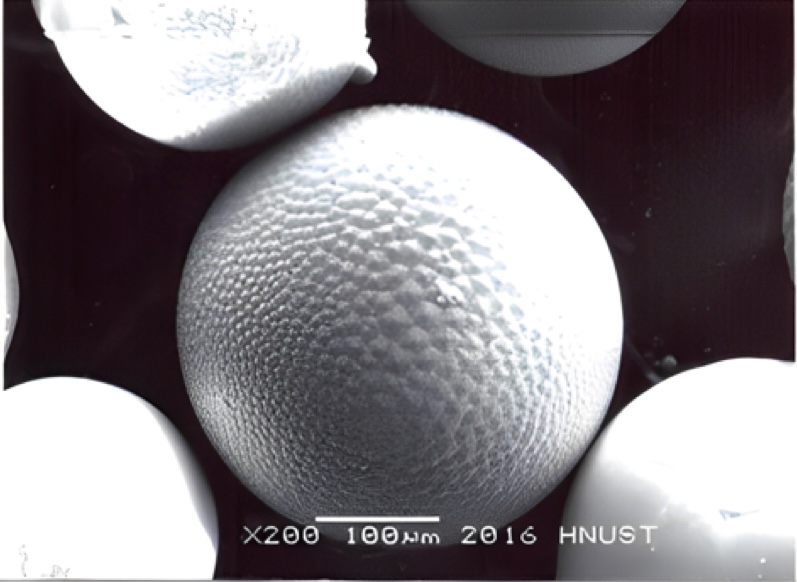
b. Alto aumento
↓ Fig.2 Diagrama de producción de arena cerámica CERAMSAND ↓
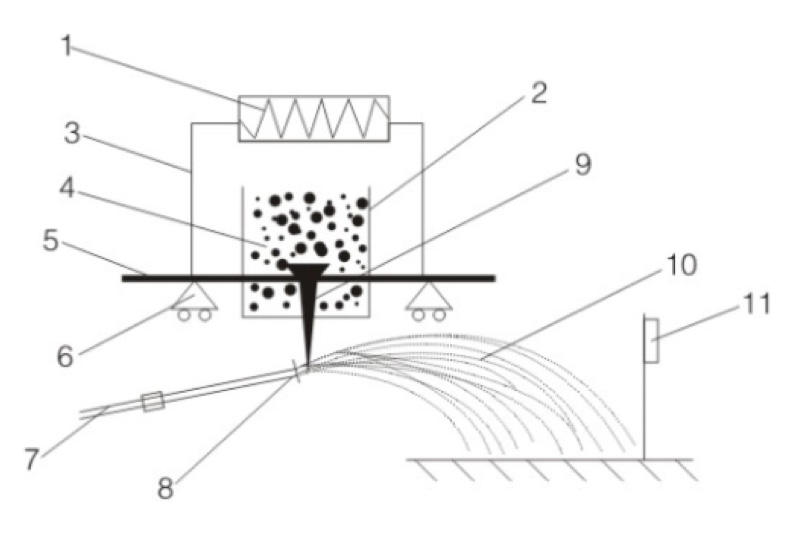
1. Transformador / 2. Cuerpo del horno / 3. Alambre de cobre / 4. Mineral de bauxita / 5. Electrodo de grafito / 6. Dispositivo de alimentación de electrodos / 7. Manguera de aire / 8. Tobera / 9. Mineral fundido / 10. Granos de arena cerámica CERAMSAND / 11. Extracción de polvo
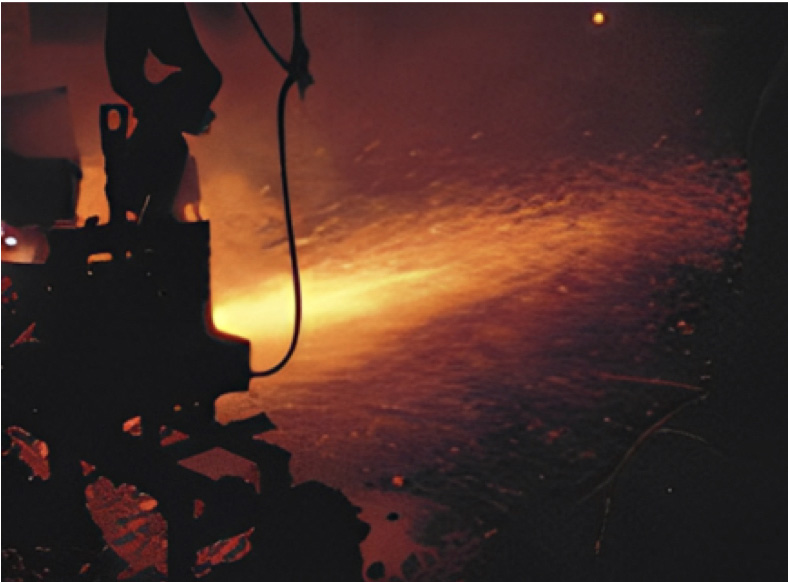
La arena cerámica CERAMSAND, por otro lado, tiene propiedades mucho mejores que la arena de sílice para obtener un mejor rendimiento en fundición. Por su composición y procesamiento únicos tiene alta refractariedad, es inerte y estable, tiene excelente fluidez, alta dureza, es resistente al desgaste y es de grano esférico. La forma redonda forma uniones de manera eficiente y requiere niveles reducidos de aglomerante. Además, en este sentido, la arena cerámica CERAMSAND tiene ventajas generales mucho mejores en comparación con otras arenas especiales, incluyendo la arena de zirconio y la cromita.
El uso de arena cerámica CERAMSAND proporciona una oportunidad para que las fundiciones reduzcan los costos de la fundición y promuevan la calidad de la fundición, así como para construir un Sistema de producción respetuoso con el medio ambiente.
2. Propiedades Físicas y Químicas de la arena cerámica CERAMSAND
Los principales componentes químicos de la arena cerámica CERAMSAND son el dióxido de aluminio y el dióxido de sílice. Después de fundirse y recristalizarse, la arena cerámica tiene una composición mineralógica de mullita, corindón y trazas de sustancias amorfas. Su refractariedad es superior a 1800℃ y es un material refractario de alúmina y silicio de alta dureza. Los colores de la arena cerámica incluyen gris pardo y negro. La Tabla 1 muestra las principales propiedades físicas y químicas de la arena cerámica CERAMSAND.
Tabla 1 Propiedades físicas y químicas de la arena cerámica CERAMSAND (típicas)
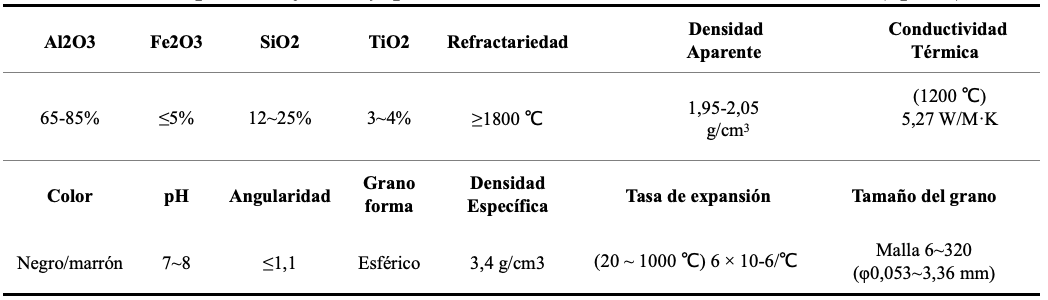
3. Características de la arena cerámica CERAMSAND
Como arena de fundición especial, la arena cerámica CERAMSAND tiene las siguientes características:
(1) La expansión térmica de la arena cerámica es muy baja, similar a la arena de zirconio. Usando arena cerámica para hacer moldes y machos, el veining, las crostas y otros defectos de expansión probablemente puede ser eliminado de las piezas fundidas.
(2) La arena cerámica tiene buena fluidez y es fácil de recubrir gracias a su forma esférica. Los moldes y machos tienen una alta permeabilidad y son fáciles de desarenar después del colado.
(3) Utilizando arena cerámica se puede ahorrar entre un 30 y un 50% del consumo de aglutinante, obteniendo piezas fundidas con buen acabado y economizando costes.
(4) La arena cerámica es un material neutro e inerte, por lo que puede utilizarse en sistemas con aglomerantes ácidos y alcalinos, adaptándose también a diversas aleaciones.
(5) La arena cerámica tiene un buen rendimiento de reciclaje y se puede recuperar fácilmente mediante muchos métodos.
(6) La arena cerámica tiene una alta refractariedad y buena estabilidad. Es especialmente adecuada para la producción de machos de arena complejos y piezas fundidas de acero y de hierro con grandes secciones.
(7) Tiene un tamaño de partícula amplio, distribución que se pueden combinar y mezclar arbitrariamente para satisfacer las necesidades específicas de los clientes.
4. Aplicaciones de la arena cerámica CERAMSAND en fundición.
Actualmente, la arena cerámica CERAMSAND se utiliza habitualmente en fundiciones de hierro, acero, acero inoxidable y no ferrosas con distintos tipos de aglomerantes, No Bake furánico, método de cáscara Croning, Cold Box, No Bake Fenólico Alcalino, proceso No Bake de silicato de sodio curado con éster y fundición de espuma perdida. A continuación, se muestra un gráfico circular del uso de la arena cerámica basado en datos recientes:
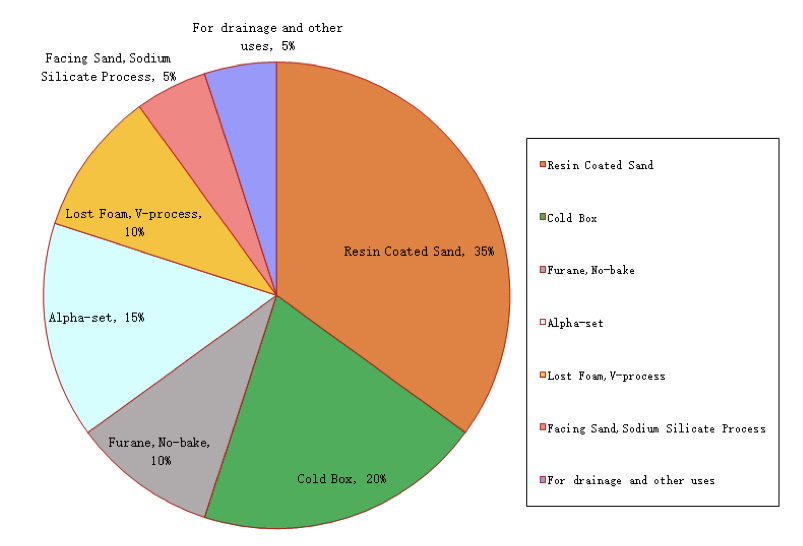
← Fig. 3. Diagrama circular de aplicaciones de arena cerámica CERAMSAND.
4.1 Proceso No Bake Furánico
En el caso de la arena cerámica aglomerada con resina furánica, las resistencias mecánicas en frío son mucho mayores que las que se obtienen con la arena de sílice. Al agregar la misma cantidad de resina, las resistencias mejoran notablemente.
Para probar la resistencia a la tracción de la arena cerámica y la arena de sílice, se utiliza una resina furánica base adicionando un 1,2% sobre el peso de las arenas y un 40% de catalizador sobre el peso de las resinas respectivamente. Las probetas se rompen a las 1, 2, 3, 4, 5 y 24 horas. Para cada fracción de tiempo se rompen 8 probetas. El resultado de la prueba se muestra en la Tabla 2.
Tabla 2. Resistencia a la tracción de la arena cerámica CERAMSAND y la arena de sílice Dalin.
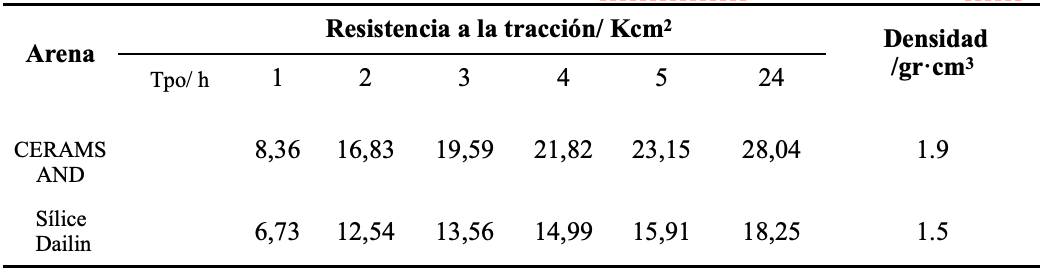
Se demuestra que la resistencia a la tracción después de 24 horas, con la arena cerámica CERAMSAND, es superior en más del 50% a la de la arena de sílice Dalin. Se ha demostrado que el uso de arena cerámica no solo puede reducir la cantidad de resina, ahorrar costos, mejorar la eficiencia de producción, sino que también reduce en gran medida los defectos de fundición como la porosidad.
4.2 Fabricación de machos procesos COLD BOX y SHELL MOLDING
Aprovechando las ventajas de la arena cerámica CERAMSAND, se pueden fabricar arenas pre revestidas de alta calidad que tienen propiedades excepcionales como alta refractariedad, baja expansión térmica, fáciles de desarenar, altas resistencias mecánicas y menor emisión de gases. Para machos particularmente complejos. (ver fig. 4a y 4b), la arena cerámica pre revestida tiene una excelente fluidez, lo que puede resolver el problema de tener un macho completamente formado.
↓ Fig.4 Machos y piezas fundidas de arena pre revestidas ↓
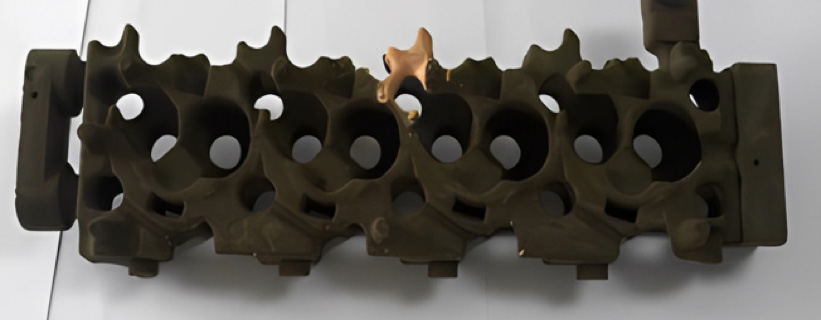
a. Macho de la camisa de agua de la culata
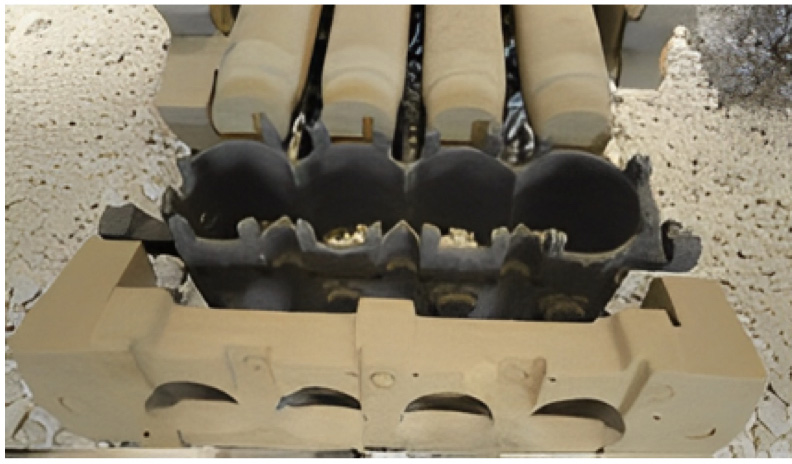
c. Conjunto de machos
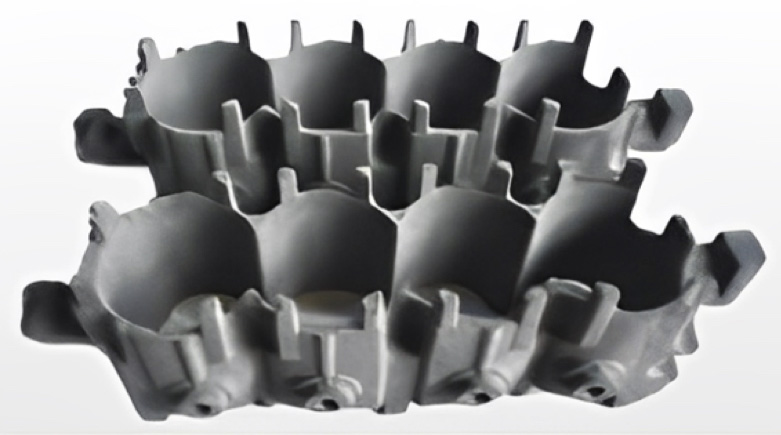
b. Macho de la camisa de agua del bloque de cilindros
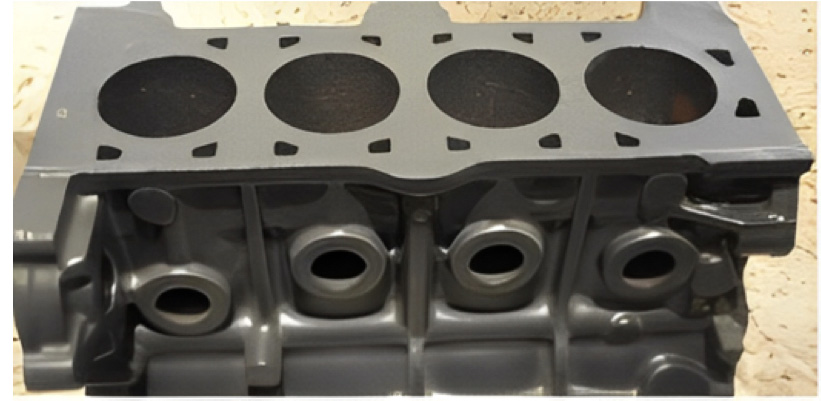
d. Bloque de cilindros
El proceso de Shell Molding con la arena cerámica (ver fig.5). El proceso de fundición es de alta eficiencia productiva, la precisión dimensional y el acabado de las piezas son excepcionales y la arena utilizada es fácil de reciclar, lo que reduce en gran medida la emisión de residuos sólidos. Los beneficios ambientales de este proceso también son notables.
Se puede predecir que, como nueva tecnología de fabricación ecológica, el proceso de fundición de cáscara, con arena cerámica, se convertirá en una nueva tecnología de fundición ampliamente utilizada.
↓ Fig.5 Moldes de Shell y piezas fundidas ↓
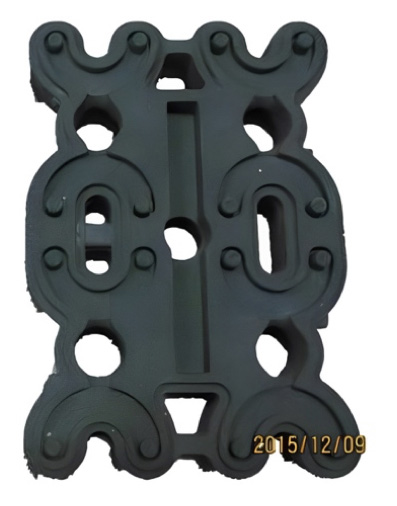
a. Pieza de macho único para el método Shell
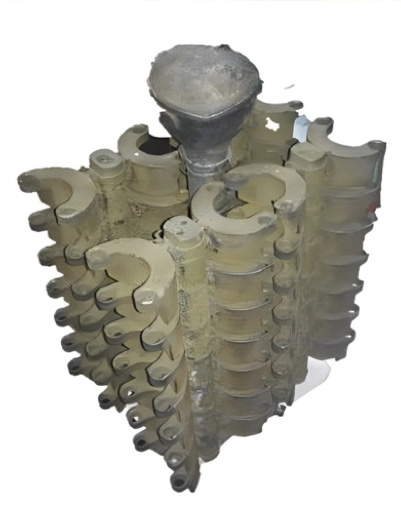
b. Pieza de macho único para el método Shell
4.3 Resina Fenólico Alcalina, moldeo y fabricación de machos
Es bien sabido que la temperatura de vertido del acero fundido es bastante alta, por lo que el uso de arena cerámica permite aprovechar al máximo las ventajas de la resina fenólico alcalina. El consumo de arena de fundición se puede reducir a 30-50 kg por tonelada. El consumo de aglutinante se reduce en un 30-50 %. Con la mejora de la calidad de la superficie de la fundición, la cantidad de trabajo de recuperación de arena y limpieza de la fundición se puede reducir en más del 60%. Puede mejorar significativamente la calidad de la fundición, reducir la tasa de rechazo y el costo de producción. También reduce la emisión de gases residuales, arena y polvo, mejora el entorno de trabajo, previene la silicosis y logra el objetivo de la producción ecológica. La figura 6 muestra machos y piezas fundidas de válvulas de alta presión de acero inoxidable fabricadas mediante el proceso Fenólico Alcalino utilizando arena cerámica CERAMSAND.
↓ Fig.6 Machos de arena cerámica con proceso Fenólico Alcalino y una pieza fundida. ↓
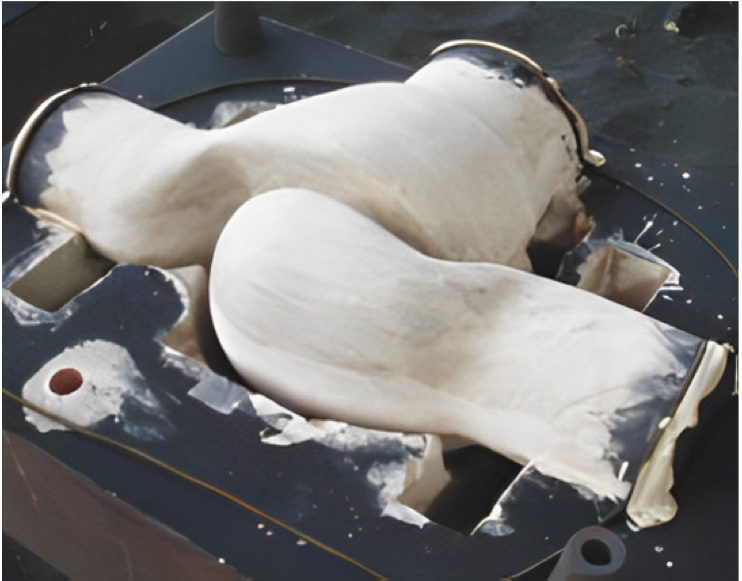
a. Moldes y machos
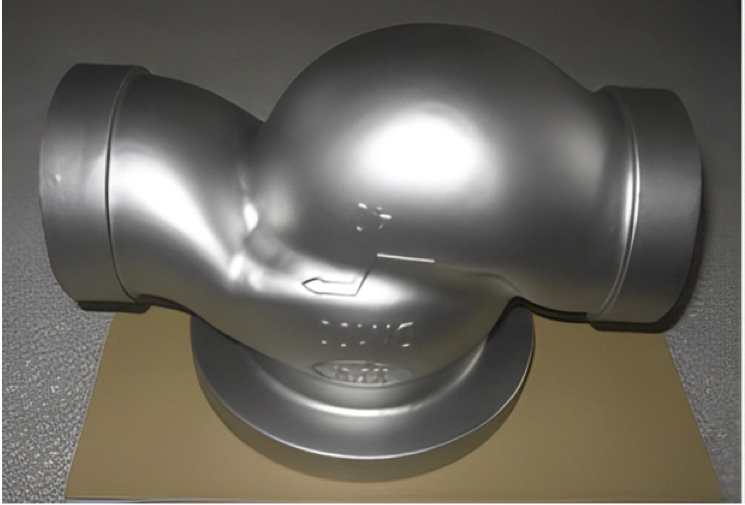
b. Fundición de válvulas de alta presión
La Tabla 3 muestra el rendimiento de resistencia de la arena cerámica en comparación con la arena sílice Dailín utilizando resina fenólico alcalina. Podemos encontrar que la resistencia a la tracción después de 24 horas es un 31% mayor que la de la arena de sílice, mientras que el nivel de aglutinante de la arena cerámica es un 40% menor que el de la arena de sílice, y la evolución del gas de la arena puede tener una reducción de 32%. En la práctica, utilizando arena cerámica, la fundición puede ahorrar el consumo de aglutinante entre un 45 y un 55%.
Tabla 3: resistencia a la tracción de la arena cerámica y la sílice Dalin con el proceso Fenólico Alcalino
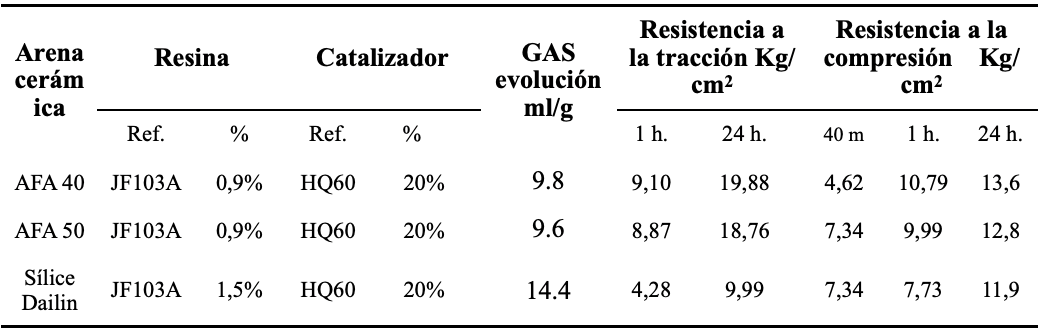
4.4 Arena aglomerada con Silicato de Sodio
En el caso del acero fundido de sección pesada, generalmente la presión estática del caldo sobre los moldes y los machos es mucho mayor durante un tiempo de vertido relativamente más largo. Las reacciones mecánicas, térmicas y químicas entre el metal y los moldes pueden ser violentas. Estas pueden provocar una penetración grave del metal y calcinaciones de arena, especialmente en las partes de intersección de las piezas fundidas. Esto requiere mucho trabajo en las fundiciones para rebarbar piezas fundidas que puedan tener un acabado deficiente y los talleres de rebarba están sujetos a condiciones medio ambientales de trabajo horribles. En algunas circunstancias, las malas condiciones de trabajo exponen a los trabajadores al peligro de silicosis.
Para resolver los problemas de penetración de metal y calcinaciones de arena, hemos realizado una prueba de producción en el sitio. Agregamos entre un 3 % y un 4,5 % de silicato a la arena cerámica, mezclamos bien y atacamos la arena mezclada en las partes marcadas «A». En los moldes que se muestran en la Fig. 7, luego añadimos arena sílice de relleno aglomerada con silicato. Después del pintado y el vertido, obtuvimos piezas fundidas sin penetraciones ni calcinaciones de arena. Esto demuestra las propiedades anti penetración de la arena cerámica CERAMSAND.
Figura 8 muestra el detalle (intersecciones de paredes, macho, etc.) de piezas grandes de acero fundido donde se utiliza arena cerámica CERAMSAND como arena de contacto. Estas zonas son propensas a las sinterizaciones, penetraciones y calcinaciones. Utilizamos arena cerámica de contacto para llenar los agujeros profundos y rectos del soporte rodillo. Los resultados muestran que esto puede no sólo reducir la penetración de metal, sino también eliminar la posibilidad de craking debido al estrés térmico causado por la mala deformabilidad térmica mediante el uso de arena de sílice.
↓ Fig.7 Posición de llenado de arena cerámica ↓
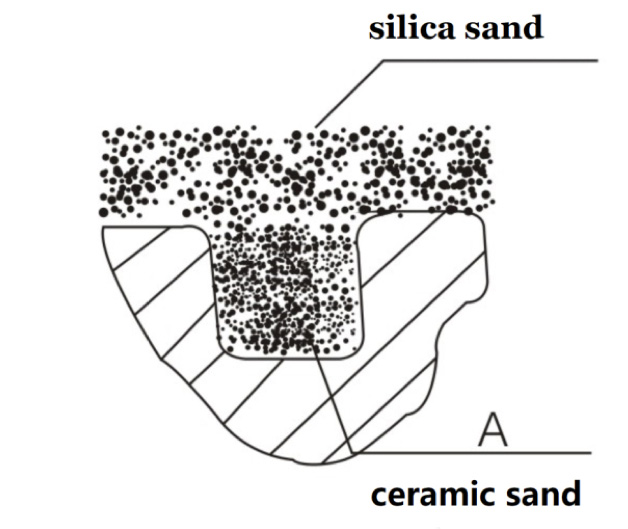
↓ Fig.8 Moldeo y fabricación de machos con silicato de sodio (Soporte de rodillos. Fundición de acero) ↓
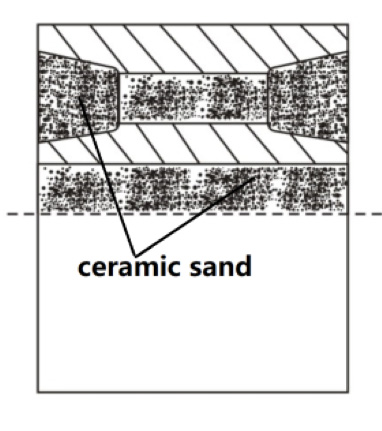
a. Posición de llenado de arena cerámica
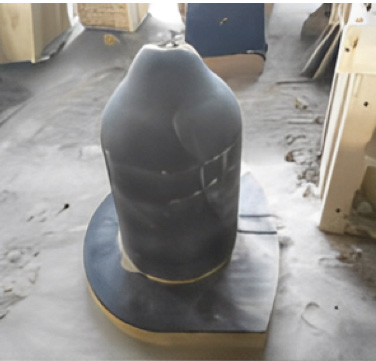
b. Se utiliza arena cerámica en la superficie del macho
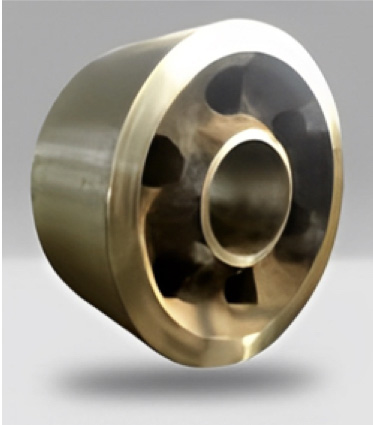
c. Rodillo de soporte (acero fundido)
En la actualidad, además de utilizar arena cerámica CERAMSAND como arena de contacto, su mezcla con cromita también puede aprovechar las ventajas de la arena cerámica y la cromita en general. Además de utilizar silicato de sodio endurecida con CO2, la arena cerámica también tiene ventajas significativas en el proceso de endurecimiento con éster. La Tabla 4 compara la resistencia a la tracción de la arena cerámica y la arena de sílice mediante el proceso de endurecimiento con éster de silicato de sodio.
Tabla 4 Resistencia a la tracción de arena cerámica y arena de sílice Dalin aglomerada con Silicato de sodio y endurecimiento con éster.
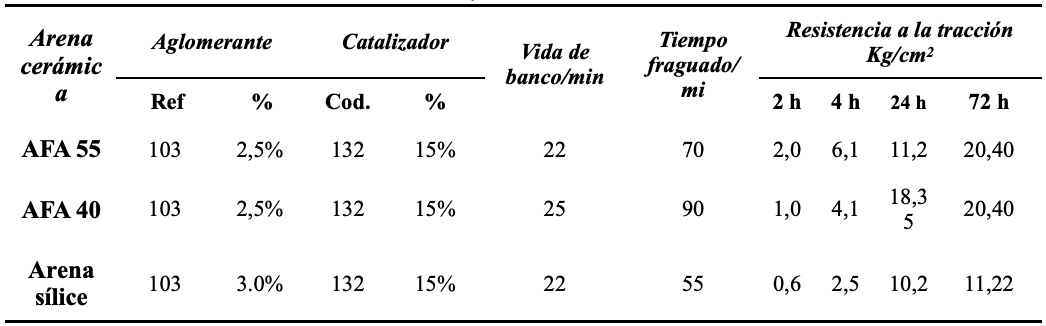
4.5 Proceso Lost Foam y proceso en V
Para el proceso de espuma perdida y el proceso en V, las fundiciones usan arena cerámica como arena de respaldo. Utilizando CERAMSAND la tasa de piezas rechazadas disminuye significativamente. El costo total disminuye. El consumo de arena de las piezas fundidas es de solo 1-2 kg por tonelada y el entorno de trabajo mejora obviamente debido a su forma redonda, buena fluidez, gran durabilidad, alta conductividad térmica, menor cantidad de polvo, etc.
Figura 9 (c) ilustra el proceso Lost Foam y un molde de un bloque motor. Cuando usas otras arenas esos agujeros de pequeño diámetro y gran profundidad difícilmente pueden ser llenados y compactados adecuadamente provocando serios problemas de sinterizaciones y penetraciones que difícilmente se pueden limpiar y recuperar. Usando la arena cerámica CERAMSAND estos problemas pueden eliminarse. La arena cerámica CERAMSAND tiene forma esférica, proporciona buena permeabilidad, tiene buena fluidez y compactabilidad. El porcentaje de rotura de la CERAMSAND durante el moldeo y la recuperación es muy bajo por lo que el rechazo de piezas es muy bajo y el rendimiento de producción puede llegar al 97%.
↓ Fig.9 Moldeo y fundición de espuma perdida ↓
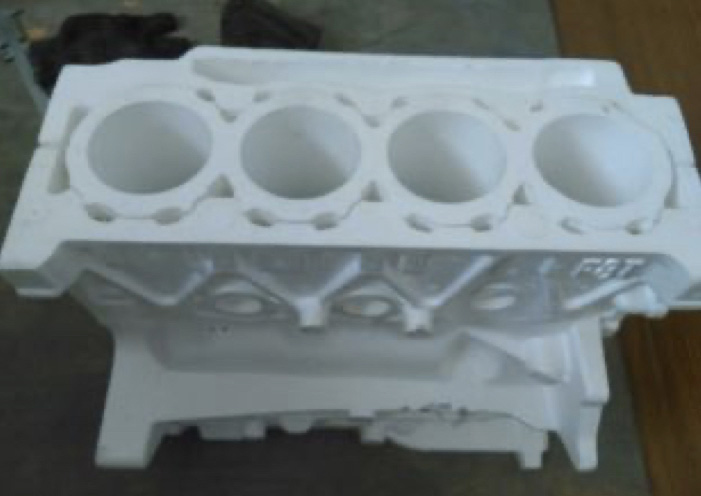
a. Modelo de espuma
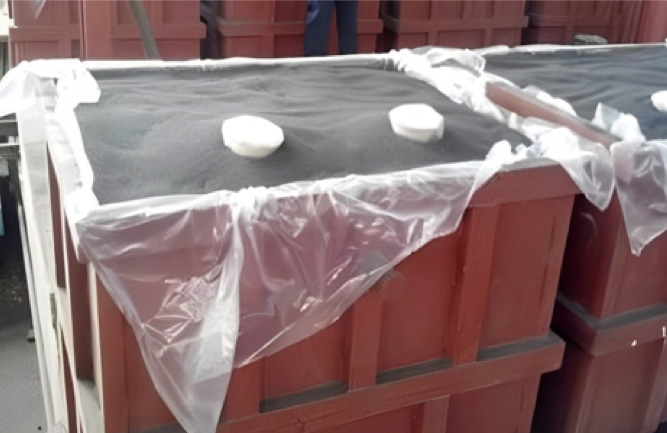
b. Moldeado con arena cerámica.
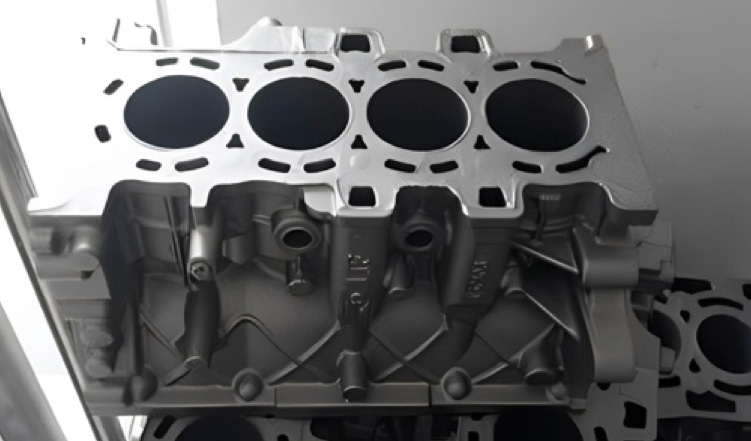
c. Un bloque de cilindros fabricado mediante el proceso de Lost Foam
Conclusión
(1) En procesos NO BAKE (incluidos sistemas furánicos y fenólico alcalinos) el uso de arena cerámica CERAMSAND puede mejorar significativamente la resistencia de la arena aglomerada y puede ahorrar el porcentaje de aglutinante en más del 30%, disminuyendo la evolución de gas y obteniendo tasas de recuperación de hasta el 98%, eliminando notablemente los vertidos a las escombreras.
(2) Al utilizar arena cerámica CERAMSAND, como arena base en los machos de arena revestida y en el método de Shell Molding, la fluidez del RCS es excelente, la tasa de expansión y la evolución de gas son bastante bajas, por lo que se reducen los defectos de gas como los pinholes y las vetas en las piezas fundidas.
(3) El uso de arena cerámica CERAMSAND, en sistemas de silicato de sodio, reduce el consumo de aglomerante mejorando las propiedades para el desarenado, evitar las penetraciones y las calcinaciones, y puede reducir el costo de las piezas fundidas.
(4) En la producción de fundición con espuma perdida, el uso de arena cerámica mejora la fluidez, la compactación de la arena, la permeabilidad, etc. Debido a la alta resistencia y la baja tasa de rotura de la arena cerámica CERAMSAND, el rendimiento de recuperación de la arena es alto y el costo es bajo.
Con rápido desarrollo de la industria de la fundición, para cumplir con los requisitos de protección ambiental, cada vez más fabricantes elegirán arena cerámica CERAMSAND como arena base, en parte o en su totalidad. La arena cerámica, un nuevo material de fundición en el siglo XXI, desempeñará un papel más importante en la nueva era del desarrollo sostenible y la fabricación ecológica.
A problemas, soluciones; nosotros trataremos siempre de conseguir aquella más eficiente en todos los aspectos.
PROYECTO TRAS PROYECTO
EUSKATFUND está en constante evolución y desarrollo. Gracias a proyectos como estos, y a los apoyos que hemos recibido, hemos conseguido ir un paso más allá en el tratamiento y resultado de los materiales que proporcionamos; nunca sin dejar de lado uno de neustros valores principales, el de estar del lado del medio ambiente siempre que sea posible.
MÁS POST QUE TE PUEDEN INTERESAR
Ampliamos un nuevo pabellón
Euskatfund abre un nuevo pabellón destinado a la fabricación de manguitos y mazarotas.
EUSKATFUND, marca registrada.
A fin de proteger nuestra imagen y establecernos como «Marca», hemos registrado Euskatfund.