USR. USR SECONDARY ATTRITION RECLAMATION
Japan, a country that imports silica sand because it lacks this natural resource, and historically a country sensitive to environmental problems, was the cradle of the development of sand recovery processes in the foundry world.
The Secondary Unit of Atriction
USR is a registered trademark of SINTO Corporation, Japan. This equipment is being manufactured, under license, by OMEGA FOUNDRY MACHINERY, Ltd., and distributed in the Spanish market by EUSKATFUND, S.L..
SINTO registered the USR and WSR models for the recovery of silica sand from the foundry, especially in moulding processes where inorganic (silicate) and semi-inorganic (alkaline phenolic resin) binders are used. Although these processes are difficult to recover, up to 90% can be recovered with the implementation of USR in the recovery process.
RECOVERY VARIETIES
⇒ WHAT IS USR?
The Secondary Attrition Unit consists of one or two attrition chambers (depending on model) with high speed bearings. The chambers are electrically controlled and the rotary action forces the sand entering the unit to be thrown to the periphery of the deck. To help remove the resin, ceramic rollers are rubbed against the sand with controlled and adjusted pressure by pneumatic cylinders fitted to the base of the unit.
The sand is retained for a short time at the top of the chamber before being evacuated or sent to the second chamber in the case of double chamber models. The sand from the second chamber is then displaced out of the chamber by the inlet of the sand from the first chamber. The treated sand that has fallen out of the second chamber is displaced through a classifier below the chamber, where a fluid bed separates the fines (mainly resin dust).
⇒ IDEAL PARAMETERS FOR PRIMARY RECOVERY (mechanical)
1. Good sand/metal ratio – 4:1 or better.
2. Iron parts.
3. Organic binders.
4. Low binder percentages.
In these cases, foundries can recover high levels of sand and maintain good sand characteristics. If you do not fall into this category, you have two options for regenerating your recovered reject sand.
These are set out below:
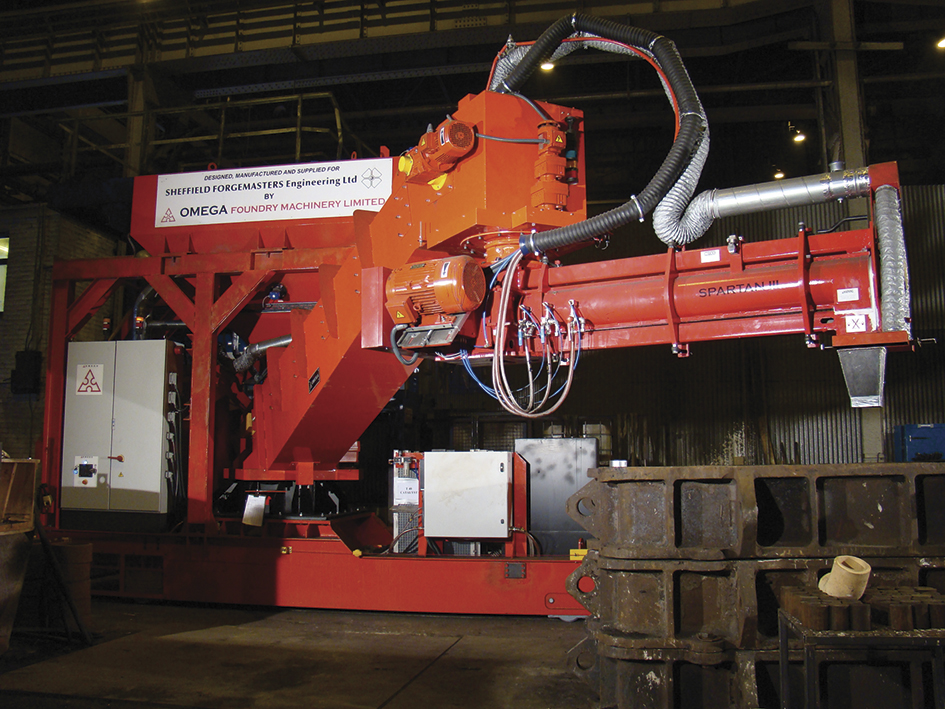
⇒ THERMAL RECLAMATION
✓ High initial cost for investment.
✓ High operating cost – energy consumption,….
✓ Cannot recover inorganic binders.
✓ Have to add an additive to recover alkaline phenolic resin bonded sand.
Some sands cannot be recovered due to changes in morphology.
✓ Requires regular emission controls to ensure that local standards are maintained.
· AGAINST THE AGREEMENT TO REDUCE CO2 EMISSIONS.
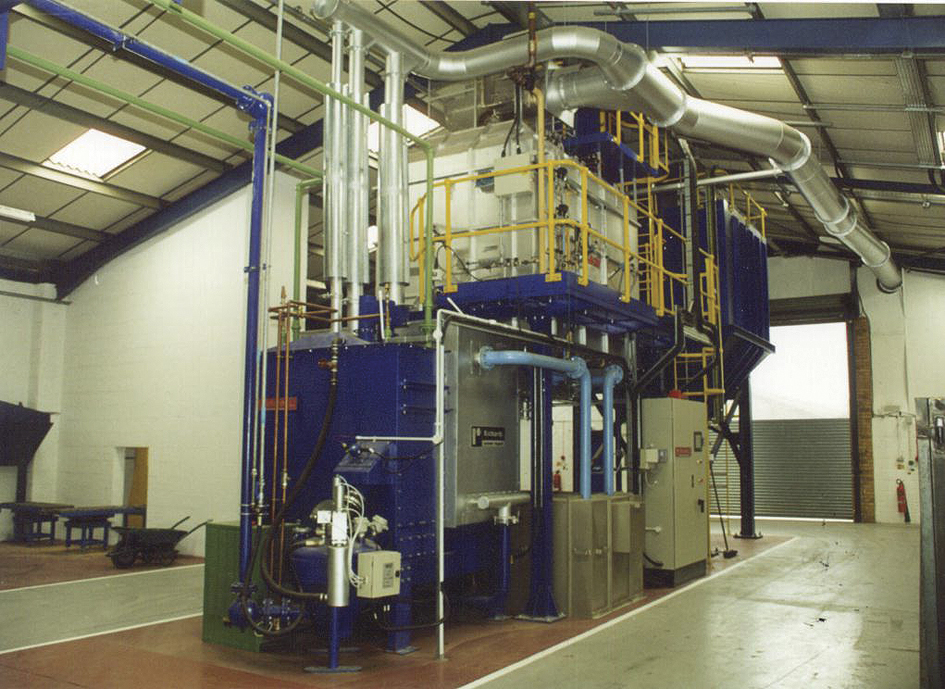
⇒ USR SECONDARY ATTRITION RECLAMATION
✓ Removes the binder content by mechanical means. Also in the case of inorganic (silicate) and semi-organic (alkaline phenolic resins) binders, without damaging the conditions and grain size.
✓ Low initial investment cost. Rapid amortisation. No CO2 emissions, as there is no gas heating.
✓ Low energy cost for its operation, contrary to what happens with thermal recovery, with a reduced cost in spare parts, since the elements of greater wear are ceramic, which guarantees a long durability (more than 3,000 hours).
✓ Control of the percentage of binder removal, adjusting various parameters (pressure on the rings, ring thickness, drum rotation speed, number of sand passes, one or two per unit depending on the model).
✓ It can work with any base sand.
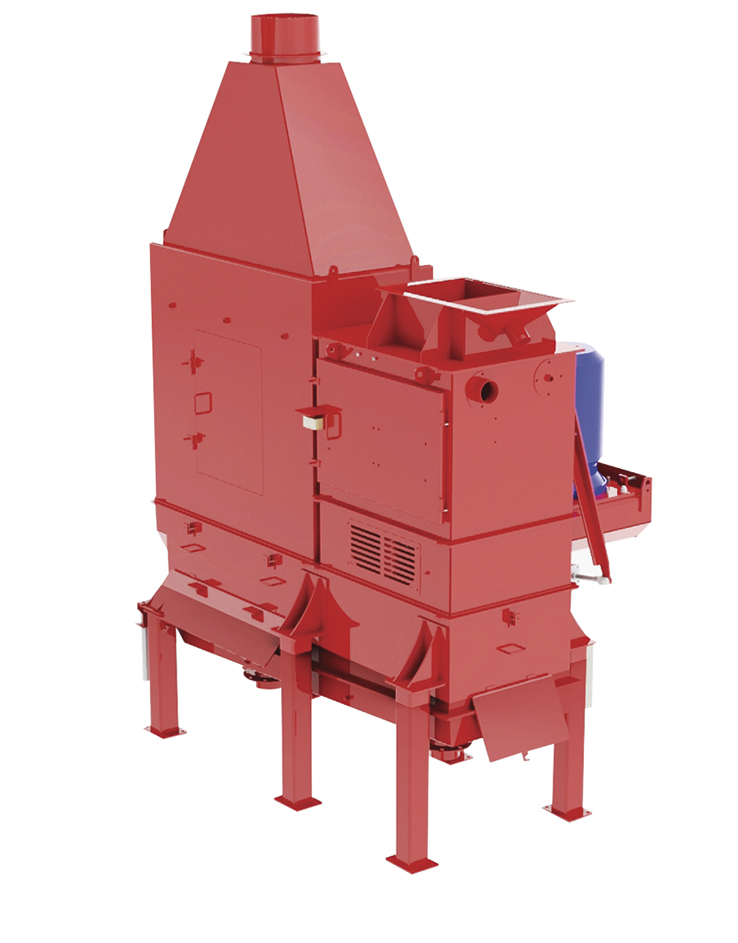
USR. MARKET SITUATION
Today, there are USR installations all over the world. Of course, Japan is the predominant country with 180 installations. In the rest of the world, 18 units have been sold in the last 2 years, despite the severe economic crisis, due to their fast amortisation, with a high rate of satisfaction among melters, helping to minimise waste and avoid CO2 emissions into the atmosphere.
This process can be costly to afford, but certainly profitable in the short and long term.
PROJECT AFTER PROJECT
EUSKATFUND is constantly evolving and developing. Thanks to projects like these, and the support we have received, we have managed to go a step further in the treatment and result of the materials we provide; never leaving aside one of our main values, that of being on the side of the environment whenever possible.
MORE POSTS YOU MAY BE INTERESTED IN
Properties & Applications of Ceramic Foundry Sand CERAMSAND
Ceramic sand has distinguished performance in foundry in compare with silica sand and other popularly used special sands. This article introduces the production process, the physical and chemical properties, and the application features of ceramic sand.
Sphere Ox, a feasible solution.
Veining, burns, penetrations and pinholes are common defects in castings and the daily struggle of foundries to control them. We tell you the solution.
FUNCTIONAL CORE SHOOTER MACHINES
Adjectives that would describe the characteristics of an efficient core shooter are: versatile, practical, comfortable, fast, economical, …
THERMAL SAND RECLAMATION
Thermal reclamation has reached a point where, thanks to its innovations, it is profitable, economical and reliable.